Ceramics and graphene open up new possibilities for bone-like materials
Graphene Flagship Partnering Project CERANEA develops graphene-filled ceramic sandwiches that deliver materials with enhanced properties and functionalities.
The mineralised structures of some bones, seashells and trees have something in common: their composition varies gradually throughout their volume, providing multiple functional roles at once. These are classified as functionally graded materials (FGMs) and can also be artificially engineered with tailored properties for numerous applications, including biomedical implants, optoelectronic devices, sensors and batteries.
The Graphene Flagship Partnering Project CERANEA was funded through FLAG-ERA Joint Transnational Call 2017 to develop FGMs with graphene in ceramic matrices. The project involves researchers at the Graphene Flagship Partners Eotvos Lorand Research Network, the Centre for Energy Research (ELKH CER, Hungary) and the Fraunhofer Institute for Ceramic Technologies and Systems (Fraunhofer IKTS, Germany), and Graphene Flagship Associate Member Slovak Academy of Sciences (Slovakia).
We speak with Csaba Balázsi, CERANEA Project Leader and scientific advisor at Graphene Flagship Partner ELKH CER, to learn more about their strategies, accomplishments and the potential application of ceramic-graphene FGMs in coatings and orthopaedics.
Which type of functionally graded materials are you studying?
FGMs are sandwich-structures made of several functional layers. We produce different stacks for novel types of composites, optimised for the desired combinations of electrical, thermal and mechanical properties.
These stacks contain graphene, hexagonal boron nitride (hBN) or other layered materials, as well as ceramics, such as silicon nitride, silicon carbide and zirconia. Graphene additives are important fillers that increase the wear resistance and conductivity of ceramic matrices. Graphene also improves the thermal quality and the ability to withstand cracking. The key lies in the careful composition of these composite materials, which defines their porosity and conductivity.
For example, we can create a sandwich-structure made with ceramics as the bottom layer, a mixture of ceramics and graphene as the intermediate layer, and a foam-like structure of graphene as the top layer. As the graphene concentration increases from bottom to top, so does the porosity and conductivity of the material.
Why are these graphene-enabled layered structures important?
Layered structures can deliver the performance desired by industry. These materials are more resistant than current ceramics against damages caused by electrical arcing, so can be used as long-lasting coatings for contacts, switches or wearable parts.
In CERANEA, we are demonstrating the feasibility of producing these coatings at an industrial-scale and in an economically affordable manner. Graphene can replace precious metals, such as gold or silver nanoparticles, leading to a more sustainable and resource-efficient fabrication. These composites will be suitable for engineering applications, such as structural health monitoring systems.
Furthermore, composites with graphene, silicon nitride or silicon nitride-zirconia are being studied as novel biomedical implants in orthopaedics. The shape, morphology and composition of natural bone vary: certain parts are denser, while others are more spongy. Similarly, varying amounts of graphene in the ceramics-graphene composite result in different porosity. For this reason, our sandwich-structures made with ceramics and graphene could be applied to bone reconstruction.
What is novel and unique about your approach?
We evaluated the concept of sandwich structures in composites in terms of synthesis procedures, functionalities and microstructures. These investigations can give new insight into the design of new-generation composites made of ceramics and layered materials, and identify possibilities for further optimisation.
We are producing graphene via conventional powder technologies, and we manufacture these FGMs with one-step sintering and hot isostatic pressing. In this way, we obtain different layers with varying compositions, from 5% to 30% graphene by weight. These show improved mechanical properties, electrical and thermal conductivity, compared to the state-of-the-art functional ceramics.
To reach the desired performance, we analysed these materials at all scales, from the macro to the micro-level. We gathered information about their morphology, components’ type and homogeneity, graphene oxidation level and porosity.
Which have been your most important achievements so far?
We devised a new method for preparing multi-layered graphene and GO starting from commercially available micro-sized graphite powder. We mill it to reduce its particle size and promote the intercalation and exfoliation of graphite into multi-layered graphene particles. This simple and efficient process leads to the production of 100 grams of multi-layered graphene in one batch, but it can be easily expanded to 100 kilograms in industrial processes. The graphene particles are then oxidised into GO using a combination of strong oxidising agents, thermal oxidising and sonication. We also carried out comprehensive morphological characterisations to reveal GO’s structure and size.
We also studied ceramics based on silicon nitride and zirconia with varying amounts of multi-layered graphene. We identified the optimal graphene, silicon nitride and zirconia ‘sandwich’ – a layer of 30% multilayer graphene (MLG) by weight sandwiched between two layers of 5% MLG. This configuration resulted in a two-to-three-fold improvement in mechanical properties, compared to the opposite ratio (30-5-30 wt% MLG). Sandwich composites are valuable models for understanding the relation between composition and structure of materials, especially in the context of potential health monitoring applications.
In our most recent publication, we used X-ray microscopy in a state-of-the-art synchrotron source to study our ceramic/graphene composites in 3d, as well as their cracking and degradation mechanisms. Our method for preparing these carbon-rich samples could be relevant for other researchers working in this field.
References
Balázsi, Katalin, et al. "Examination of milled h-BN addition on sintered Si3N4/h-BN ceramic composites." Processing and Application of Ceramics 12.4 (2018): 357-365.
https://doi.org/10.2298/PAC1804357B
Furko, Monika, et al. "An economic and facile method for graphene oxide preparation from graphite powder." Resolution and Discovery 4.1 (2019): 21-25.
https://doi.org/10.1556/2051.2019.00066
Lamnini, Soukaina, et al. "Influence of structure on the hardness and the toughening mechanism of the sintered 8YSZ/MWCNTs composites." Ceramics International 45.4 (2019): 5058-5065. https://doi.org/10.1016/j.ceramint.2018.11.207
Lamnini, Soukaina, et al. "The role of the attrition milling on the grain size and distribution of the carbon nanotubes in YSZ powders." Boletín de la Sociedad Española de Cerámica y Vidrio 58.3 (2019): 126-133.
https://doi.org/10.1016/j.bsecv.2018.10.001
Hanzel, Ondrej, et al. "Highly electrically and thermally conductive silicon carbide-graphene composites with yttria and scandia additives." Journal of the European Ceramic Society 40.2 (2020): 241-250. https://www.sciencedirect.com/science/article/pii/S0955221919306727?casa_token=DoREdFReyVAAAAAA:uQozDQKzN1a-TtYBX1yZG9gbT1orKHOo0XcUxHXm7lwl0eE-uBCN4n82IVhR86Oecqc3QSn37fc
Balázsi, K., et al. "Porous sandwich ceramic of layered silicon nitride-zirconia composite with various multilayered graphene content." Journal of Alloys and Compounds (2020): 154984. https://www.sciencedirect.com/science/article/pii/S0925838820313475
Balázsi, K., et al. "Graphene added multilayer ceramic sandwich (GMCS) composites: Structure, preparation and properties." Journal of the European Ceramic Society (2020). https://www.sciencedirect.com/science/article/pii/S0955221920300649
Liao, Zhongquan, et al. "Microstructure and Fracture Mechanism Investigation of Porous Silicon Nitride–Zirconia–Graphene Composite Using Multi-Scale and In-Situ Microscopy." Nanomaterials 11.2 (2021): 285. https://www.mdpi.com/970146
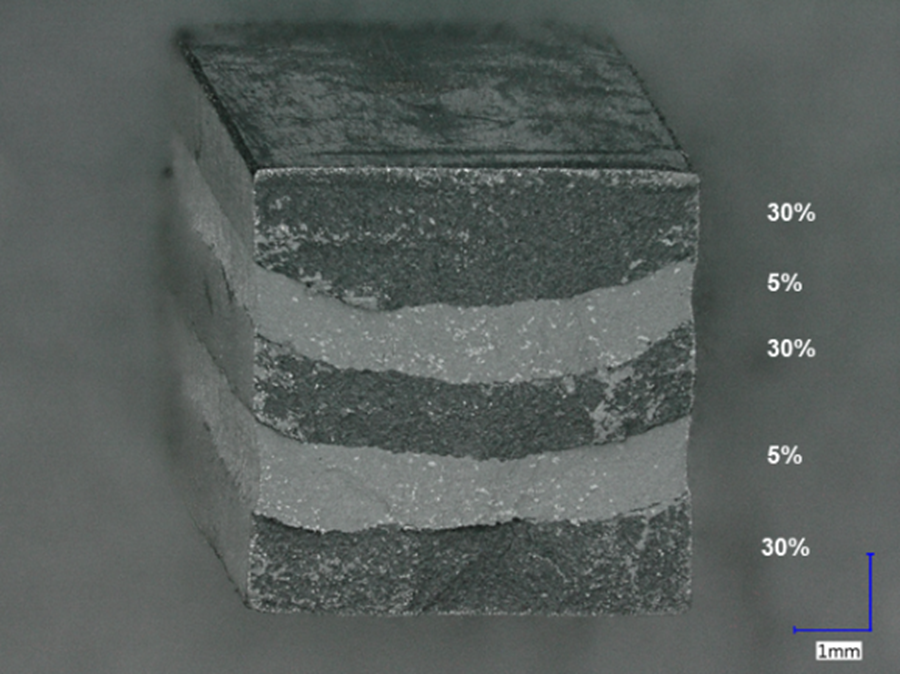
Sintered sample made of five-layered Si3N4/graphene composite with 5% or 30% graphene by weight. Credit: CERANEA