Graphene for Composites Applications
Nathan Feddy is the business developer for composites applications for the Graphene Flagship. Feddy gained key experience in the financial and nanotechnology consultancy sectors prior to joining the team at The University of Manchester’s state-of-the-art Graphene Engineering Innovation Centre (GEIC). He has worked with several high-profile companies to incorporate graphene into their composite materials/products, to provide multi-faceted performance improvements and additional enhancements. Feddy now offers his thoughts on the current state of graphene in composites applications.
Q. What is the current state of graphene for composites applications?
Graphene and related 2D materials have attracted substantial investment and resources over the last decade for their development into the next generation of composite materials. This is due to the potential of these nanomaterials to act as reinforcing additives capable of simultaneously imparting significant mechanical property enhancements as well as embedding multi-functional benefits on the host matrix. As graphene and 2D materials are still in their infancy, the relative maturity of different types of composite systems are not uniform. Therefore, some nanocomposite systems are already commercially available and others are not developed enough to launch to the market.
A significant focus has been devoted to producing thermoplastic and thermosetting systems with amalgamations of a range of mechanical and functional properties. These include; improved strength and stiffness, increased thermal and electrical conductivity, enhanced barrier properties, fire retardation and others. Progress has been made in identifying and developing the appropriate incorporation processing techniques capable of delivering these property enhancements. Indeed, in this area a number of companies have already started/are close to launching graphene enhanced thermoplastic and thermosetting materials to market. This is a promising area in the near term as the underlying processing technologies have reached the required level of maturity and there is little need for additional equipment for prospective manufacturers. This knowledge and the low capital expenditure requirements result in minimal barriers to entry.
The incorporation of graphene related materials into conventional elastomeric compounds can significantly augment a number of their desirable properties. Traditionally in certain elastomer components, there was a need to trade off/compromise between the wear resistance and application specific functionality. The addition of graphene has been shown to enhance the properties of the elastomer to the extent that the wear resistance and performance functionality can both be greatly improved. Additionally, the improvement of the materials' electrical and thermal conductivity is beneficial for a number of their applications. Some graphene enhanced elastomers are commercially available and have been processed into products. These include high performance sport shoes, bicycle tyres, recycled mats and many others.
Inorganic composites including ceramics and metal matrix composites is another promising materials sector with significant potential to benefit from graphene and related materials. Academia has shown that a plethora of mechanical and functional benefits could be achieved in suitable inorganic composite systems. These benefits include; improved hardness, enhanced fracture toughness, increased strength and stiffness, superior wear resistance and conductivity. There are many applications for these nanocomposites in a range of industrial sectors. The incorporation and processing techniques for these materials have not yet reached the same level of maturity as the aforementioned systems. Considering the combination of 'market pull' and 'academic push' this area could also be very promising in the near future.
Q. What challenges does graphene face in becoming integrated in composites?
The term "composites" encompasses a vast range of different material technologies each of which have distinct processing procedures and production parameters. Each of these systems bring their own unique technical challenges to ensure appropriate 2D material incorporation. The following are some of the key technical and logistical challenges facing graphene and other 2D materials in the composite domain area.
In order to achieve the desired reinforcement, the nanomaterials must have the appropriate microstructure and interfacial properties to promote ideal bonding and stress transfer with the matrix. The challenge is identifying the right graphene material capable of providing the desired reinforcement for the specific system. Graphene materials available on the market can differ greatly in terms of their lateral size, aspect ratio, defect density and surface functional groups. Materials often require modification in order to alter the aspect ratio and lateral dimensions as well as functionalization procedures to ensure that the appropriate chemical groups are available for effective matrix bonding. This is a significant challenge, there is no one solution that fits all, and therefore it is a challenge for material scientists to constantly iterate.
A validation service was launched by some members of the Graphene Flagship which could provide some independent authentication and assessment of different graphene material supplies, the consistency of supply and performance in the variety of relevant material systems.
Additionally, to attain the potential property enhancements, the incorporation process of the nanomaterials into the matrix system is often critical. Achieving a homogeneous dispersion and ideal orientation of the nanomaterial is a particular challenge for the relevant range of composite materials and is often affected by the interfacial interactions. Graphene's reinforcement abilities are dependent on the number of layers and therefore in some systems it can be beneficial to use high shear processing techniques to exfoliate and disperse the materials in situ. This opportunity is not available in other systems due to the phases and processing procedures deployed. It is often necessary to apply pre-processing treatments to the 2D materials prior to dispersion to ensure they are in a state capable of achieving the enhancements.
By this point in the interview, you are starting to understand the complexity of engineering these nanocomposite systems and the myriad of parameters involved. An additional challenge is solving the knowledge gap in the 2D materials space. As mentioned before, the composites sector spans a wide range of materials industries each of which will have unique opportunities, technical issues and novel solutions. A challenge for the composites sector is identifying the people and projects with the expertise to drive the nanocomposite field forward. Organizations such as the Graphene Flagship therefore exist to extend the network of nanotechnologists and academics with their partners.
One of the unique selling points of graphene to the composites industry is that significant property enhancements can be achieved at low nanomaterial loadings, often in the range of 0.1-5 weight percent. This is also beneficial as graphene is still a relatively expensive material and therefore the loadings must be low enough that a financial margin is present. Although the loading levels are low, some application areas such as the concrete industry for example, use millions of tons of material annually. Even at low loadings of 0.1 weight percent, in order to be applied at scale, manufacturers would need more than the current global graphene production capacity. A challenge for the industry is to ensure that the production capacity is in place and consistent enough for the scale up of bulk composite materials applications.
Finally, but not exhaustively, certain composite manufacturers operate in highly regulated application areas. They may often face individual and unique challenges in introducing new nanomaterials into their existing products. This is a more nuanced issue; however, organizations and experts are often available in each field to guide companies to drive their products through the regulatory process and into the market.
Q. What are the most promising graphene composites products currently on the market?
Graphene enhanced composite products have been launched to market in a number of different application areas. Many of these products have been successful in gaining market share and providing application specific enhancements relative to their conventional alternatives. The following are some of the promising graphene enhanced composite products on the market in accordance with their application areas.
In the automotive sector a number of products are now commercially available from a range of suppliers. Graphene enhanced polyurethane foams were produced by one supplier that are more thermally stable, reduce cabin noise (improved acoustic attenuation) and improved mechanical properties. This component has now been incorporated into over a million cars. One company already has graphene enhanced carbon fibre pre-pregs available for purchase. A high-end sports car manufacturer has produced a track car with graphene enhanced composite panels using these pre-preg material systems. The incorporation of graphene improves the strength and allows the manufacturer to greatly reduce the weight. This should simultaneously improve the application performance and reduce fuel consumption/GHG emissions.
The high-end sporting equipment sector has also seen some disruptive graphene composite products launched into their market. A tyre manufacturer has produced graphene enhanced elastomer bicycle tyres to enhance the performance and improve the wear resistance. One company has successfully launched a range of graphene enhanced sports shoe products tailored for activities such as running and hiking. Another company was able to produce graphene enhanced mats from 80% recycled rubber with the properties of the virgin material. A number of companies have launched graphene enhanced sporting goods such as tennis rackets and fishing rods. They have capitalised on the enhanced strength and stiffness from the nanomaterial additives to reduce the components weight and improve the performance.
The built environment/construction sector is also starting to see products launched to market and high profile in situ testing for certain systems. One company has produced a graphene enhanced bitumen composite for longer enduring road surfaces. This has the potential to greatly improve road quality by reducing pothole incidence, which in turn should reduce maintenance costs and associated injuries. Graphene enhanced coatings for the protection of composite systems have been developed and launched to market by a number of producers which could greatly reduce corrosion degradation. Graphene enhanced concrete products are not yet commercially available; however, this is a promising product due to the significant environmental and financial savings that could be achieved with nanomaterials.
This is not a comprehensive list of available graphene products and many more promising developments will be launched in the near term.
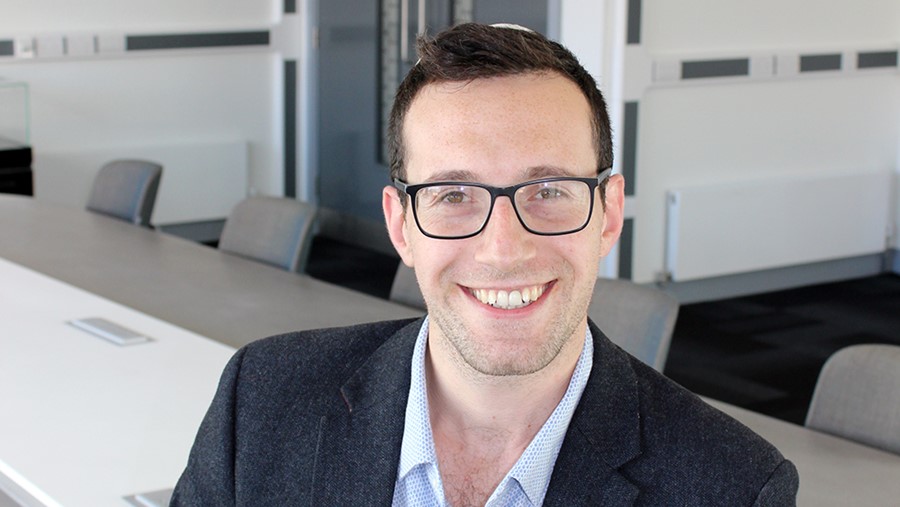
We interview Nathan Feddy, our Graphene Flagship business developer for composites applications.