Flash Graphene: Trash to Treasure
The applications for graphene use are broad, having altered the composition of electronics, energy storage and biomedical devices, sensors and composites and coatings over the past two decades. This is all due to its exceptional mechanical, electrical and thermal properties. However, what are the environmental impacts of its use and how does the cost limit its application?
Graphene was first isolated in 2004, and since then the cost has come down significantly. However, this is still dependent on the quality of the graphene desired, and the production methods used to isolate it. Commercial-grade, high-quality graphene can still be extremely expensive, with retail prices ranging from $60,000 to $200,000 per ton.1 In some instances, the cost is high (both economically and environmentally) due to the resources needed to produce it.
A promising discovery made by scientists at Rice University in the lab of chemist James Tour, in January 2020, may upend our graphene production processes and our concept of trash altogether. Their findings were first published in Nature (2020) and describe the use of Flash Joule Heating (FJH) to create flash graphene or flake graphene (FG). The process uses inexpensive carbon sources, such as coal, discarded food, rubber tires, plastic waste, etc. to make FG which is suitable for use in bulk composites of plastic, metals, plywood, concrete and other building materials.2 The electrical cost is about 7.2 kilojoules per gram, which is just “a fraction of the cost used by other bulk-graphene producing methods,” says Tour.3
This inexpensive process of turning trash into treasure is a simple flash of super-hot electricity focused on the source of carbon, which reorders the atoms and creates graphene. Since its discovery there have been many promising plans and proposals for its use, all with the aim of reducing carbon emissions and waste. These include building materials for the construction sector, end-of-life vehicles, plastics and municipal waste.
Construction
As populations and urbanisation thrive, the construction industry faces tremendous challenges when it comes to reducing its carbon footprint, especially the footprint linked to cement-based products.
According to an article in Forbes (2020), concrete is only second to water, as the most consumed product in the world, with the production of cement producing 8% of the world’s carbon emissions. Taken together, “if all the cement in the world was reinforced with graphene, the subsequent savings in concrete manufacture would be the equivalent of stopping the annual carbon emissions of Brazil.”4
This is where graphene can enter the equation. As a strong, but light material it can be added to concrete, and in small increments of 0.03% which then increases its compressive strength by 25%.4 Graphene-enhanced concrete is 2.5 times stronger and four times less water permeable than standard concrete. It uses much less cement to deliver the desired strength.5
By integrating graphene into concrete, engineers and architects can create structures that require less material, while still achieving the same structural performance as traditional concrete. As a result, it is expected to reduce CO2 emissions by 30%.5
End-of-life vehicles
Another top carbon emissions contributor is the automotive / transportation industry. These emissions are not only from vehicles in use, but also from the end-of-life vehicle (ELV), in the form of non-recyclable waste in the form of plastics (ELV-WP).
According to a Nature (2022) article, “the automotive sector produces an estimated 5% of the global industrial waste in the form of ELV” which is only estimated to increase as global standards of living increase, and the cost of entry decreases. Although global processing standards vary from country to country, in the United States as of 2020, an estimated 10-30% of total vehicle weight is saved from shredding. “EVL waste plastic (EVL-WP) is the largest non-recycled material in vehicles, and the increased use of next-generation polymer composites exacerbates recycling of ELV-WP through traditional methods which generally focus on singular plastic sources.”1 For instance, the Graphene Flagship partner Nanografen, based in Turkey, transforms old tyres into graphene-based nanoplatelets through a process of pyrolysis, chemical and thermal treatments.6 This offers not only a solution to the issue of toxic tyre waste, but a low-cost graphene source for thermoplastic applications in automotive components.7
The difficulty and cost of upcycling depolluted, dismantled and shredded end-of-life plastics still remains, and has made EVL-WP a pressing environmental concern, however, with the introduction of FJH and FG the possibility of processing the waste into useable graphene is hopeful.
Additionally, the Graphene Flagship spearhead project, G+Board features conductive patterns, sensors and devices based on multi-functional graphene or reduced graphene oxide to replace copper that is currently used in car dashboards.8 This substitution reduces the number of production steps and lowers vehicle weight, while also improving aesthetics and recyclability.
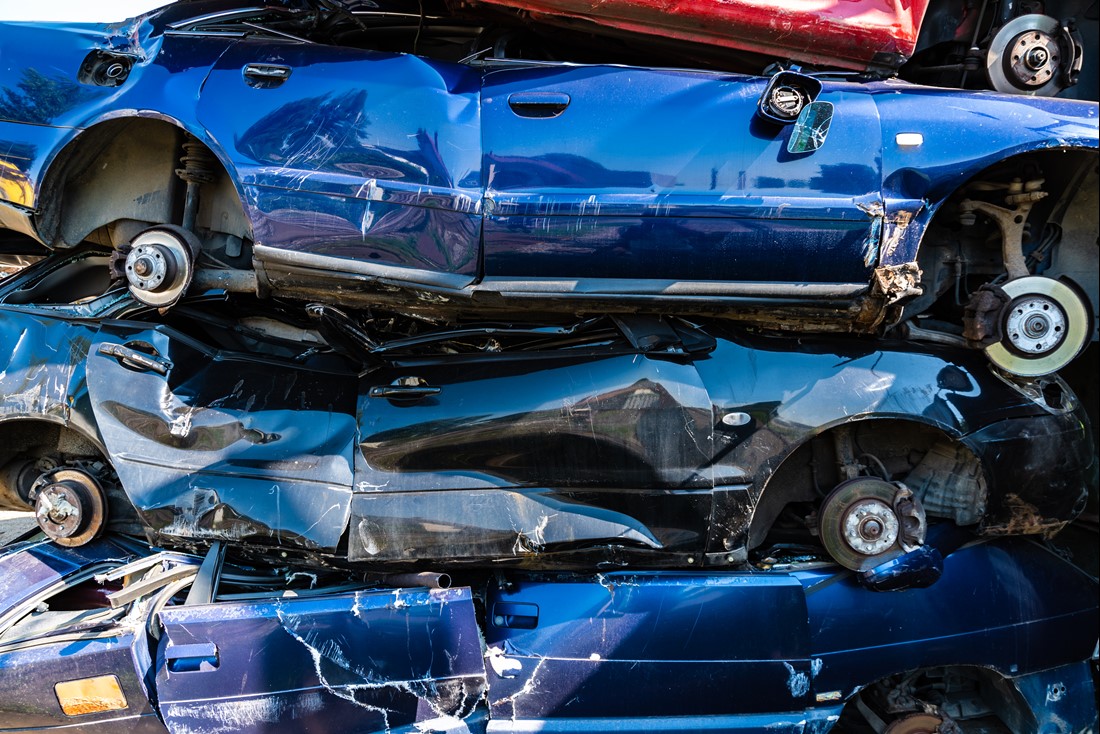
End-of-life vehicles (ELV) that can by recycled in a better way
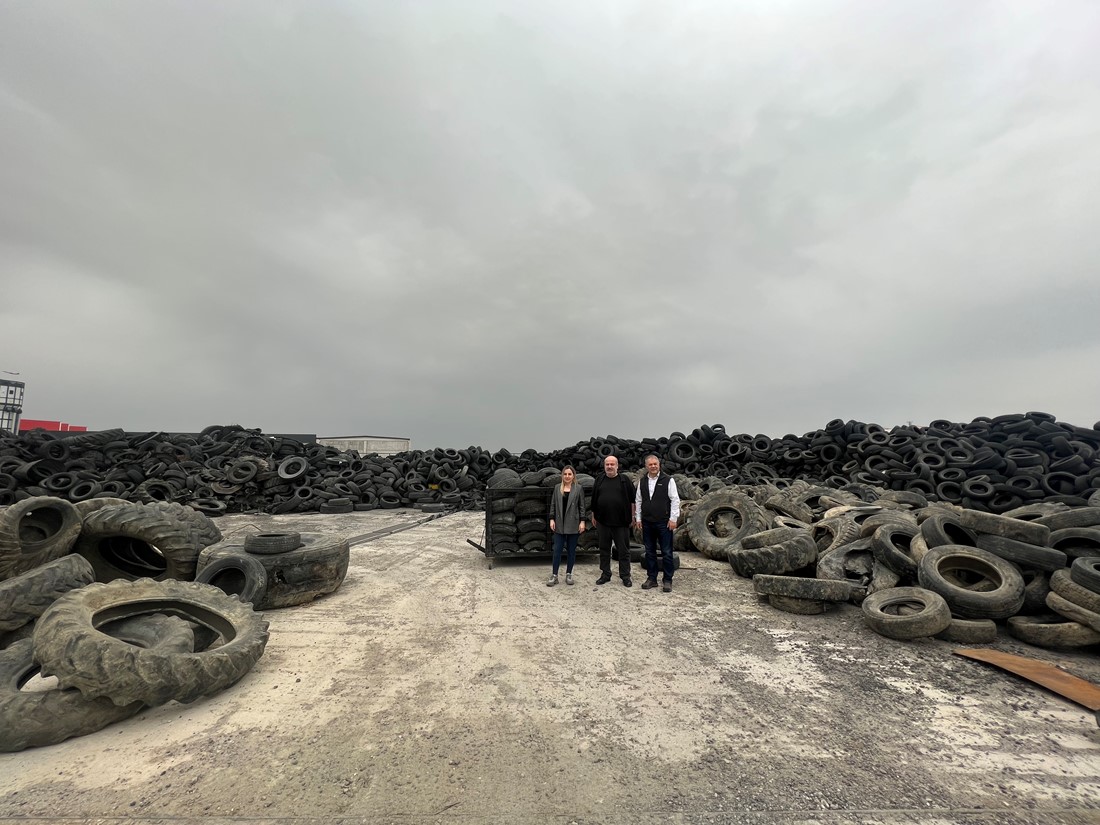
Professor Burcu Saner Okan of Nanografen among the tyres
Plastics
The problem of plastic is familiar to anyone visiting the grocery store or an open beach. It is everywhere and inescapable.
Plastics are made of polymetric materials and are used in many indispensable applications throughout our daily lives, but their long-decomposition time has left the unsolved problem of trash in its wake. Although some plastics can be recycled, most end up in landfills or floating in our seas, taking hundreds (if not thousands) of years to decompose.
Since the Rice University discovery of FG, some have begun to ponder and test whether the conversion of plastic waste (PW) to graphene could be an answer to overcoming this immense problem.
One approach to upcycling PW relies on FJH to convert PW to FG. According to findings in an ACS (2020) article, “to make high-quality graphene, a sequential alternating current (AC) and direct current (DC) flash is used. The FJH process requires no catalyst and works for PW mixtures, which makes the process suitable for handling landfill PW.” The authors also suggest that not only could FJH manage PW from landfill, but that the energy required “is ∼23 kJ/g or ∼$125 in electricity per ton of PW, potentially making this process economically attractive for scale-up.”9
Another promising use for PW could be to produce not only graphene, but hydrogen, an alternative to fossil fuels. Researchers from Rice University found that when using FJH they can transform PW into hydrogen gas, producing FG as a byproduct. The current methods for making hydrogen “either generate too much carbon dioxide or are too expensive.”10 However, by using FJH and PW they can produce clean hydrogen for free, by selling the graphene at a fraction of its current market value.9 “Hydrogen could be the green fuel of the future.”11
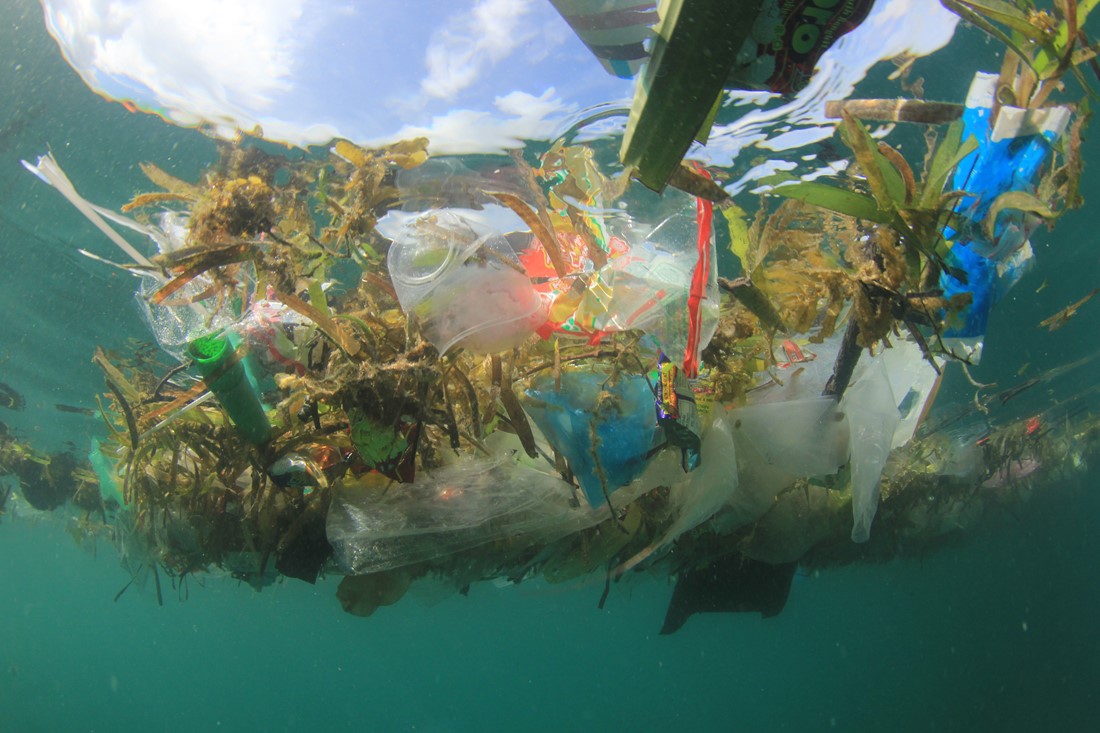
Plastic pollution in our environment
Municipal waste
With over 2 billion tons of municipal solid waste (MSW) generated globally every year, equating to “around 70% of waste ending up in landfills or open dumps... technologies that can minimise waste volume or convert waste into valuable products are required.”12 In an ACS publication, the use of FJH to make FG as a waste management strategy is assessed as a form of “waste valorisation” one which could “help achieve near-zero waste and an economy-boosting MSW management system.”12
The paper also points to this method as less polluting than its conventional counterparts, used to produce bulk-graphene, which can be resource intensive and polluting.
“Graphene research has steadily increased, and its commercialisation in many applications is becoming a reality because of its superior physicochemical properties and advances in synthesis techniques.”12
Crude Oil byproduct (asphaltene) into graphene composite
Rice University researchers have also uncovered a potential use for asphaltene a byproduct of crude oil production, that when flashed turns into useful turbostatic graphene that can be used in composites for thermal, anti-corrosion and 3D-printing applications.13 These applications tie into the Graphene Flagship project GIANCE which works to support, develop and advance innovative solutions to environmental challenges thus establishing a holistic, integrated and industrial-driven platform for the design and scalable fabrication of the next generation of recyclable graphene and 2D materials-based multifunctional composites, coatings, foams and membranes.14
Conclusion
The Flash Joule Heating (FJH) process has been shown to produce high-quality flash (flake) graphene (FG) that can lessen the carbon and water footprint by more than 90%, compared to other bulk-graphene production methods; not to mentioned that it’s more cost effective than other retrieval methods.15
However, according to a One Earth (2022) article “the sustainability credentials of the FJH approach remain unclear, and it is far from certain whether FJH can use biomass waste to produce industry-quality graphene.” Although the lab results from this study resulted in high-quality FG that could be carbon neutral when the FJH process is powered by renewable energy. In addition, they found the estimated cost to be one-fifth that of conventional graphene. Overall, their study revealed “that the FJH technology can contribute greatly to the environmental and economic sustainability of graphene production, with the potential to facilitate the transition of circular bioeconomy by valorising biomass waste.16
While there is still much research to be done, the resounding message is clear; we need new ways to minimise carbon emissions and to deal with waste, and the process and production of FG could be one way to turn our trash into treasure.
References
- Wyss, K.M., et al. Nature. 2022, https://doi.org/10.1038/s44172-022-00006-7
- Luong, D.X., et al. Nature. 2020, https://doi.org/10.1038/s41586-020-1938-0
- https://news.rice.edu/news/2020/rice-lab-turns-trash-valuable-graphene-flash
- https://www.forbes.com/sites/scottsnowden/2020/07/24/ground-breaking-method-to-make-graphene-from-garbage-is-modern-day-alchemy/?sh=874fa6d50d7a
- https://graphene-flagship.eu/materials/news/materials-of-the-future-graphene-and-concrete/#:~:text=By%20integrating%20graphene%20into%20concrete,water%20permeable%20than%20standard%20concrete
- https://www.nanografen.com.tr/products.html
- https://graphene-flagship.eu/materials/news/nanografen-is-making-automotive-vehicles-more-eco-friendly-here-s-how/
- https://graphene-flagship.eu/about/first-10-years/spearheads/c3-sh02-gboard/
- Algozeeb, W.A., et al. ACS Nano. 2020, https://doi.org/10.1021/acsnano.0c06328
- https://news.rice.edu/news/2023/making-hydrogen-waste-plastic-could-pay-itself
- https://singularityhub.com/2023/10/08/how-flash-heating-plastic-waste-could-produce-green-hydrogen-and-graphene/
- Barbhuiya, N.H., et al. ACS Nano 2021, https://doi.org/10.1021/acsnano.1c07571
- https://news.rice.edu/news/2022/rice-turns-asphaltene-graphene-composites
- https://graphene-flagship.eu/focus/composites/giance/
- Dhali, S., et al. Science Direct. 2023, https://doi.org/10.1016/B978-0-323-90914-3.00004-8
- Jia, C., et.al. One Earth. 2022, https://doi.org/10.1016/j.oneear.2022.11.006