Life cycle assessment of graphene and related materials
Graphene Flagship researchers published three studies related to the sustainable production of graphene related materials (GRMs) and their Life Cycle Assessment (LCA)
From coconut shells to discarded batteries, graphene can be produced using a range of carbon sources and a variety of methods. What are the most sustainable options? What lessons can we learn for the development of graphene-enabled products when considering the environmental impact of their life cycle? Which data are available and which are still missing? To answer these questions, Graphene Flagship researchers published three studies related to the sustainable production of graphene related materials (GRMs) and their Life Cycle Assessment (LCA) – the best tool to evaluate the environmental footprint of a product or material.
“It is very important to discuss sustainable development of advanced materials already at the early stages of their commercial exploitation,” says Cinzia Casiraghi from the Graphene Flagship Partner, University of Manchester, UK. “The integration of graphene-enabled products in everyday life needs to be compatible with the circular economy principles”.
From waste to graphene
Researchers from Graphene Flagship Partner University of Manchester, UK, and colleagues from the University of Milano-Bicocca analysed 88 studies on the production of graphene-derived materials starting from different carbon-rich waste.
Plant- and animal-derived waste, including paper cups, wood, leaves, sugarcane bagasse, coconut shells, food waste, sugar and chitosan, are abundant and have low intrinsic value, hence there is a great interest in using them to generate new sources of income. Plant-derived waste contains a high quantity of polysaccharides (e.g., cellulose, lignin) which makes them suitable for the graphitization processes.
Non-biological sources, such as coal, fuel oil and polymers, can also be used to make graphene products, but the processes typically require a pre-treatment step at a temperature above 900°C and/or the use of acids. Non-biological waste includes graphitic waste materials, such as graphite from discarded batteries. These can be recycled to prepare graphene oxide flakes, yielding materials with similar characteristics to those obtained from non-recycled graphite.
The Graphene Flagship researchers concluded that the majority of GRMs prepared from waste sources have some defects and contamination issues. Amongst all waste sources, graphitic materials are the easiest to process and exfoliate, but residual contamination is still a concern.
Environmental impacts of graphene-related materials’ production processes
Beyond waste recyclability, Graphene Flagship researchers have also reviewed the global emission and energy demand of GRMs’ different production methods. These can vary depending on choice of reactants, solvents and processing parameters. For this reason, even small adjustments in the manufacturing process can decrease the environmental footprint of GRMs.
For example, the environmental impact of chemical oxidation/reduction and exfoliation techniques can be significantly improved through higher acid and solvent recovery rates. Chemical vapour deposition (CVD) methods can become more sustainable through higher heat transfer efficiencies and more efficient consumption of precursor gases (ideally derived from renewable feedstock, such as biomass). The environmental footprint of GRMs’ growth on silicon – an energy-intensive process by design – benefits from the use of renewable energy sources.
“LCA allows us to identify opportunities for improvement and technological benefits. For example, our analysis shows that the use of waste materials as carbon sources plays a rather small role in the whole process. One should also consider the energy cost of high-temperature treatments, and the scarcity, cost and environmental impact of reagents and solvents in order to establish adequate green methodologies,” says Rosa Cuéllar-Franca from the Graphene Flagship Partner, University of Manchester.
The study also highlights the need to improve the type and quality of data associated to graphene production. This will be more and more important to compare different production routes and applications, as graphene reaches the market.
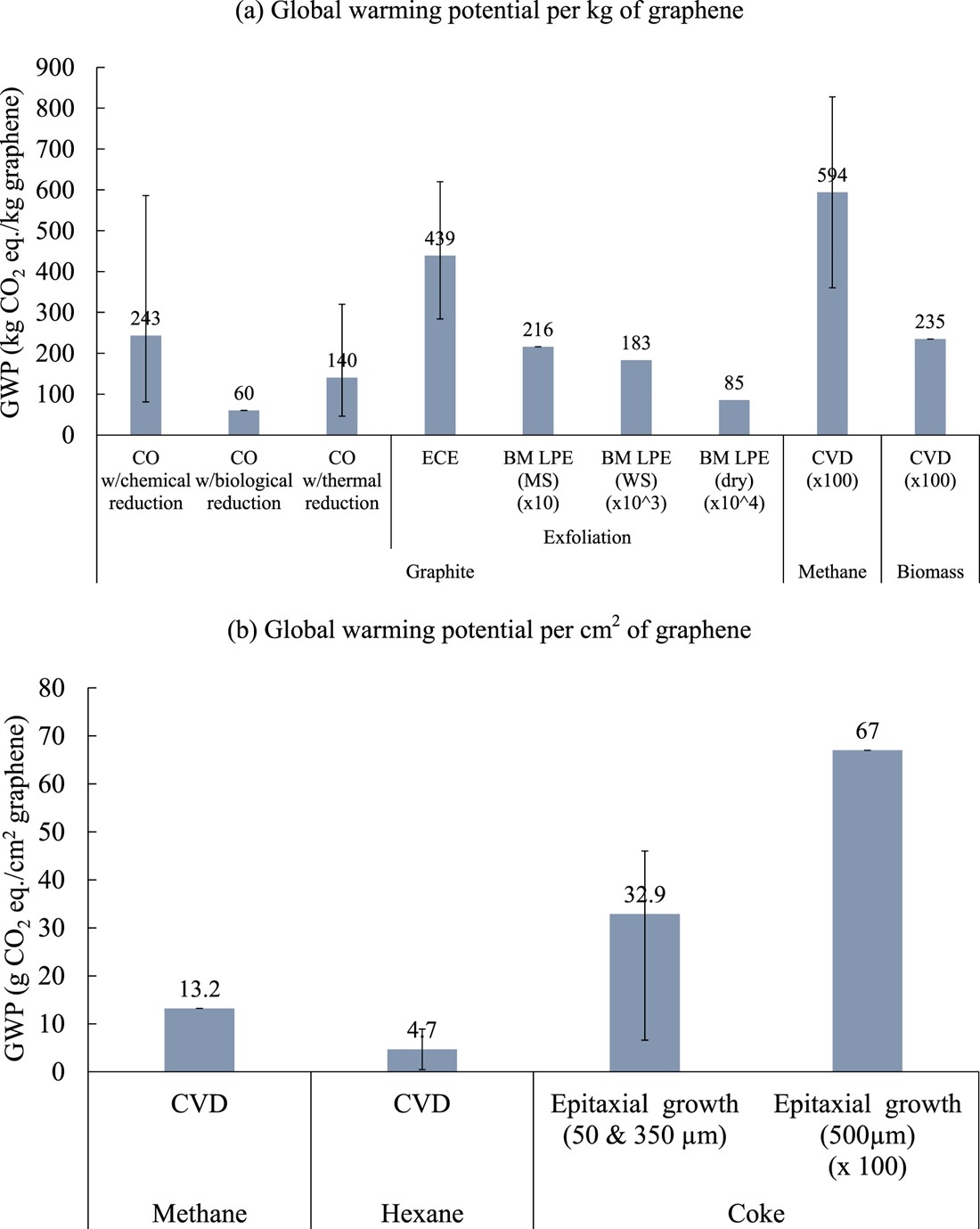
Global warming potential (GWP) for several graphene production processes, expressed (a) per kg graphene and (b) per cm2 graphene. Ball milling (BM) results are reported in melamine solution (MS), water solution (WS) and on a dry basis. Epitaxial growth results are reported in terms of the SiC wafer thickness. CO: chemical oxidation; ECE: electrochemical exfoliation; LPE: liquid phase exfoliation; CVD: chemical vapour deposition [Reference 1].
Graphene Flagship material scientists work closely with LCA experts
In another study, LCA experts of Graphene Flagship Partner EMPA, Switzerland, measured LCA-relevant data for the ball milling process – a method to exfoliate graphite into few-layer graphene. They compared 38 lab-scale pathways to produce single and few layer graphene and graphene oxide. They focused on cradle-to-gate LCA, which considers the sustainability of a product from its resource extraction (cradle) to the factory gate, before it reaches the consumer.
“Our analysis shows that graphene-based materials can be environmentally beneficial in some applications, but there is a need for more accurate data on manufacturing steps to identify the most interesting options,” says Didier Beloin-Saint-Pierre from Graphene Flagship Partner EMPA.
LCA applied to the first graphene-enabled solar farm
Researchers from Graphene Flagship Partners Hellenic Mediterranean University in Greece, University of Rome Tor Vergata, Greatcell Solar Italia SRL, IIT, National Research Council and BeDimensional S.p.A. in Italy evaluated the cradle-to-gate LCA and environmental profile of the first solar farm, based on perovskite solar panels enabled by graphene and other layered materials.
The team demonstrated the commercial potential of this technology in terms of both energy and environmental performance. The environmental footprint is lower than the present European electricity mix, and even better than some of the energy mix scenarios foreseen by the Europe energy roadmap 2050.
“Conducting an LCA based on data obtained in outdoor operating conditions in Crete, provides strong evidence of the low environmental impact of these solar panels. Our findings, combined with the evaluation of the energy yield, enable the accurate assessment of the manufacturing readiness level of this technology, driving the creation of competitive know-how for Europe,” says Emmanuel Kymakis, from the Hellenic Mediterranean University in Greece.
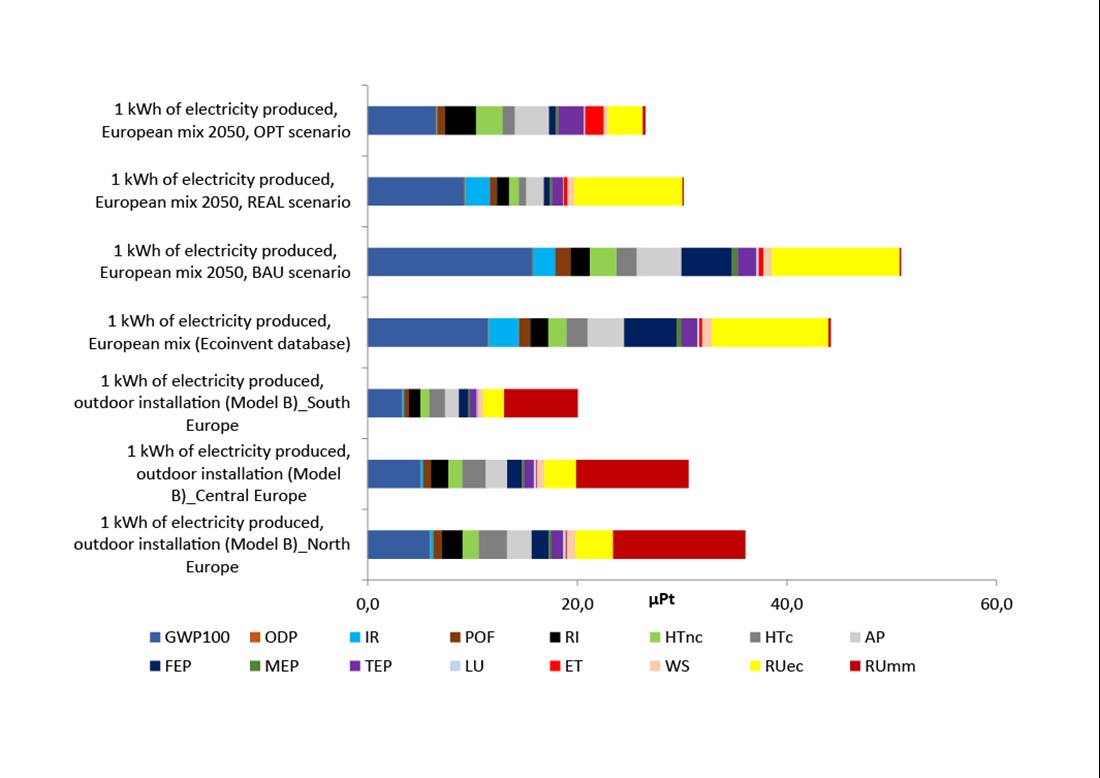
Environmental footprint of optimised graphene-enabled solar farm (Model B) if installed in North, Central and South Europe, current European electricity mix (Ecoinvent), and 2050 European electricity mix based on business-as-usual (BAU), realistic (REAL) and optimistic (OPT) scenarios. Perovskite-graphene panels installed in South Europe have the lowest environmental impact. The Environmental Footprint 2.0 method used to perform LCA considers the following 16 environmental categories: Climate change (GWP100), ozone depletion (ODP), ionising radiation (IR), photochemical ozone formation (POF), respiratory inorganics (RI), non-cancer human health effects (HTnc), cancer human health effects (HTc), acidification terrestrial and freshwater (AP), eutrophication freshwater (FEP), eutrophication marine (MEP), eutrophication terrestrial (TEP), land use (LU), ecotoxicity freshwater (ET), water scarcity (WS), resource use, energy carriers (RUec) and Resource use, mineral and metals (RUmm)[Reference 2].
“LCA provides an extremely important set of data for new products. These three studies pave the way for future research into the best way to produce and use graphene for the benefit of people and the environment,” says Maurizio Prato, Leader of the Graphene Flagship Health and Environment Work Package.
Andrea C. Ferrari, Science and Technology Officer of the Graphene Flagship and Chair of its Management Panel, adds: “These Graphene Flagship Life Cycle Analyses are the starting point to evaluate all upcoming products based on graphene and related materials. Yet again the Graphene Flagship paves the way in a necessary, but often overlooked, area of investigation, crucial to enable sustainable devices in the ever growing applications enabled by these materials”
References
- Munuera, Jose, et al. "A review on sustainable production of graphene and related life cycle assessment." 2D Materials1 (2021): 012002. https://iopscience.iop.org/article/10.1088/2053-1583/ac3f23/meta
- Beloin-Saint-Pierre, Didier, and Roland Hischier. "Towards a more environmentally sustainable production of graphene-based materials." The International Journal of Life Cycle Assessment 26, 327 (2021). https://link.springer.com/article/10.1007/s11367-020-01864-z
- Pescetelli, Sara, et al. "Integration of two-dimensional materials-based perovskite solar panels into a stand-alone solar farm." Nature Energy (2022): 1-11. https://www.nature.com/articles/s41560-022-01035-4