Metals and graphene: a new direction for innovation
Graphene Flagship Partner Graphmatech AB strives to develop graphene composite materials for metals, polymers and additives.
The grease used in metal-to-metal joints suffers from several issues: it stiffens with age, dries out, has a narrow temperature window, and moves away from the contact point. For these reasons, graphene-based self-lubricating coatings can save businesses money on maintenance and repair. Graphene Flagship Spearhead Project Circuitbreakers aims to prototype the first graphene-enabled self-lubricating circuit breakers, and solve the number one problem with low-voltage circuit breakers: grease.
The Project involves researchers at Graphene Flagship Partner ABB Corporate Research, Chalmers University of Technology, Graphmatech AB in Sweden, Nanesa SRL and the University of Rome Tor Vergata in Italy, the University of Manchester in the UK and FORTH in Greece.
We had the pleasure to talk with Mamoun Taher, CEO at Graphene Flagship partner Graphmatech AB, an award-winning Swedish graphene materials technology company. Selected as one of the hottest technology startups in Sweden by NyTeknik two years in a row, Graphmatech was also named Nordic Nanotech Company of the Year in 2018.
Why did you decide to join the Graphene Flagship Spearhead Project Circuitbreakers?
In this project, we aim to develop and scale up the production of metal-graphene composites through bulk sintering approaches and electroplating processes. Self-lubricating circuit breakers will not only solve the issues with grease, but also enable secure, continuous operation of critical facilities, such as energy generation sources, hospitals and data centres. We believe our competence and experience with metal-graphene composites can provide a valuable asset to the project’s success.
We are very proud to be part of this Spearhead Project and partner of the Graphene Flagship, the ideal ecosystem for the growth of graphene technology, providing an essential platform in which academia and industry can innovate and collaborate, creating opportunities for leadership within the graphene industry.
When did you start to work with graphene, and why?
For any materials scientists or engineers, graphene represents a dream material, since it combines a range of interesting properties. I started to research graphene as an additive to improve the properties of silver-based electrical contacts while doing a post-doc at Graphene Flagship Associate Member Uppsala University and Graphene Flagship Partner ABB Corporate Research Centre. Being at the intersection between academia and industry has enlightened me in what it takes to turn research into business and transform an invention into something of value to the market.
I read that Aros Graphene® was your founding product. How did you get the idea to develop it?
Graphene’s tendency to agglomerate (or clump together) created challenges. I put my attention to solving this issue, and in 2017 I invented a hybrid ionic graphene material that keeps graphene flakes separated. This is now patented and trademarked as Aros Graphene®.
This invention earned me the prestigious Swedish King’s scholarship for science, technology and environment, the SKAPA Prize 2020 for the Uppsala Region, as well as the Peter Egardt's scholarship in 2021.
Who can benefit from your products?
Suitable application areas include additive manufacturing, electrical contacts, thermal management, electronics, automotive and aerospace applications, where high engineering performance and lightweight are crucial.
We are currently focusing on three main business areas: metal-graphene composites, polymer-graphene composites and graphene-based additives for energy storage applications. We are working with a range of industrial partners, who are interested in making their materials stronger, more conductive. Others are focused on improving their product’s tribological properties, which are related to friction, wear and lubrication. For example, now we are targeting the functionalisation of metal powder with graphene for the powder metallurgy sectors including, but not limited to, metal injection mounding, hot isostatic pressure (HIPing), metal extrusion and additive manufacturing.
Please can you tell us about your recent accomplishments in coating copper powder with graphene for additive manufacturing?
The world electrification is driving the demand for copper to unprecedented levels. Its price keeps increasing, and the need for innovative, resource-saving electrical conductors is higher than ever before. Reinforcing copper with graphene and utilising 3d printing can improve the mechanical and functional properties of copper, so less material is needed for the same technical performance.
Printing copper using selected laser melting is challenging, due to its high reflectivity. Ensuring graphene can survive the process of metal 3d printing adds a further level of complexity. Graphehe Flagship partner Graphmatech, together with Graphene Flagship Associated Member Uppsala University addressed those two challenges through our unique coating technology.
Our coating technology was found to reduce reflectivity, thus improve laser absorption, by 67%. This, in turn, enables 3d printability of copper in a wider range of laser powers and with different laser melting machines, which to date has presented a big challenge for the 3d printing of pure copper.
Which are your plans and vision for the future?
Today we can manufacture around two tonnes per year, and are currently in the process of scaling up our production capacity to around eight tonnes per year. We have a quality control system that all manufactured batches undergo, and are currently in the process of obtaining ISO certifications. We take the development of standards in graphene very seriously, and are proud to be part of the Swedish Institute for Standards (SIS) Nanotechnology Committee, helping influence future standards, nationally and globally.
We are on a mission to build a world-leading, successful and impactful technology company that contributes to making the world a better place. Together with our valued partners, we are working to create graphene materials, which will enable an electrified and more sustainable future, while helping address the issues of grease in circuit breakers and the scarcity of copper.
Top: microscopy image of metal powder functionalised with graphene. Credit: Graphmatech
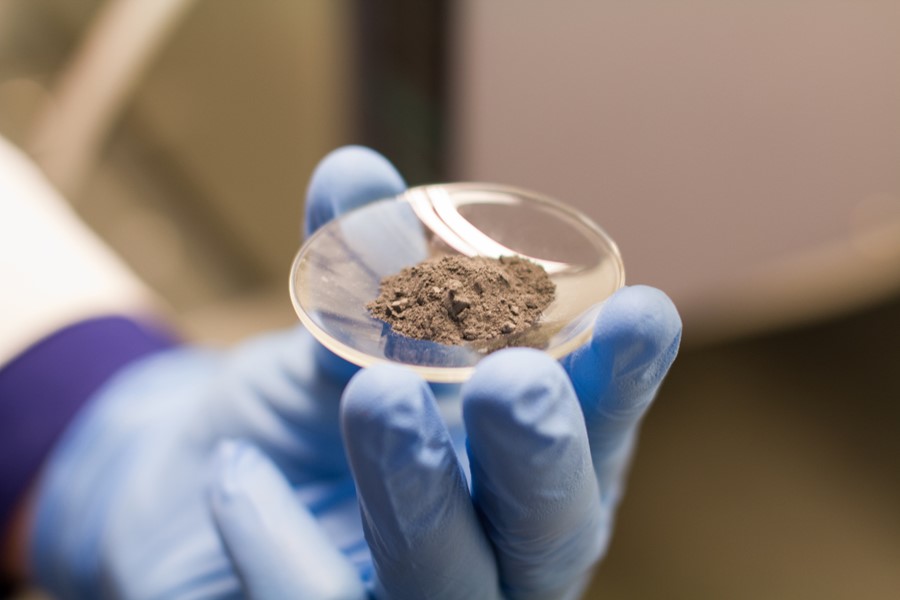
Graphmatech’s awarded product Aros Graphene.® Credit: Graphmatech
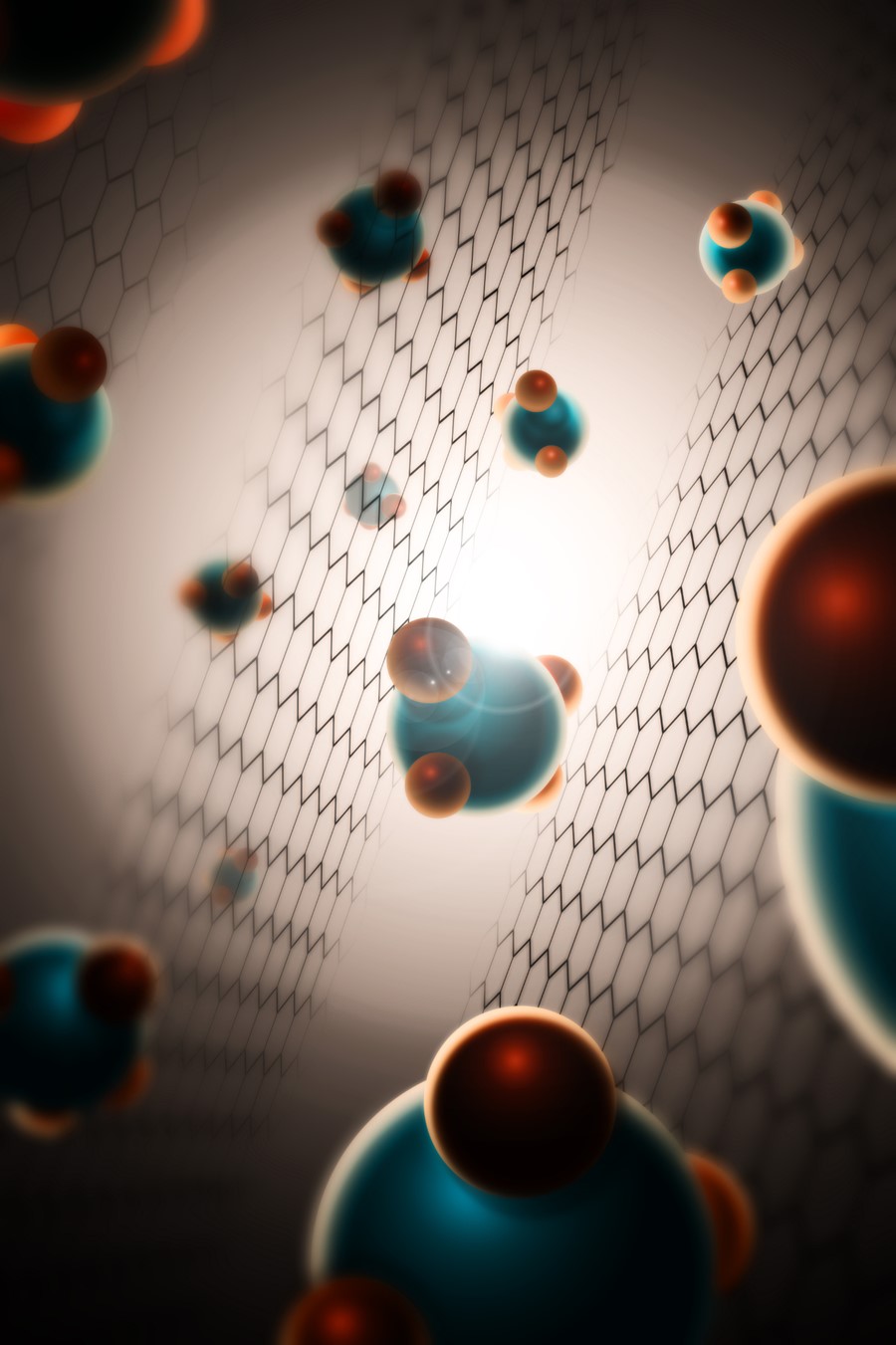
A 3D illustration of Aros Graphene.® Credit: Graphmatech