The quest to standardise commercial graphene
The Graphene Flagship's Standardisation Committee seeks to define a set of consistent and reliable standards for graphene over the years to come.
Christian Punckt is a senior researcher at Graphene Flagship partner Karlsruhe Institute of Technology, Germany. He tells us that, not surprisingly, most of the commercial graphene sold online does not comprise ideal, two-dimensional flakes of single-layer graphene. In fact, the overwhelming majority of online suppliers sell flakes under the name 'graphene' with little-to-no consistency in terms of thickness or purity.
This is because there are no universal standards dictating the quality or number of layers that a material needs to satisfy in order to be sold as graphene. Without these standards, there is no regulation of the market, so industries about to make their first foray into the field must be careful when purchasing raw materials from online suppliers.
Established standards can catalyse innovation, increase efficiency and reduce costs, lower risks, and improve the likelihood of a product making it to the market. The lack of standards in graphene is therefore a significant hindrance to graphene research and innovation, and must be addressed. Punckt stresses the importance of the Graphene Flagship's Standardisation Committee: an initiative seeking to define a set of consistent and reliable standards for graphene over the years to come.
For the full list of committee members, please see our Standardisation Committee webpage.
What is standardisation?
Standardisation is paramount in science. When research institutions and industries purchase a material from their suppliers, they need to know what they are getting: even slight differences in factors like purity, size distribution and doping can significantly change the performance and function of their products.
"Suppliers typically standardise materials using round robin tests," begins Punckt. "Before a supplier can sell their material on the market, they first send several batches of samples out to a few partner institutions. The partners each test the batch using their in-house methods, according to protocols defined by the supplier, collecting data on key material parameters." The supplier then collects the test results and compares them.
If they all show the same results, within error, this indicates that the material batch is consistent and standardised. But if there are discrepancies, then something is wrong with either the testing protocols or the batch. The supplier can then use this information to identify the source of the problem and repeat the tests until they achieve consistency.
Standardising graphene
When it comes to graphene, discrepancies in the consistency and quality of a starting material can have vast effects on product performance. Applications such as sensing and energy storage, for instance, demand a starting material with the correct proportion of dopants and contaminants. Lithium ion batteries, for example, require a certain proportion of lithium impurities, and the presence of undesirable impurities can impair the device's conductivity and cause problems such as side reactions, which hinder the movement of electrons and reduce the device's lifetime.
On the other hand, manufacturers of polymer composites need graphene that interacts favorably with their polymer matrix. These scientists are more interested in its chemical properties, or its ability to be modified and functionalized before being mixed into a composite material.
It is therefore evident that understanding key control characteristics such as these is vital for scientists to innovate using graphene. So why, then, is the standardization of commercial graphene so difficult to achieve?
Tackling the challenge
The first hurdle is the lack of a universally agreed-upon definition. "The technical definition of graphene is simply monolayer carbon: a one atom-thin sheet of carbon atoms," Punckt says. Ideal monolayer graphene is the focal point of many of the Graphene Flagship's Work Packages and Spearhead Projects, and is the key to graphene's emergence in the multibillion-Euro photonics and electronics markets. But producing monolayer graphene on a large scale is expensive, and for many researchers, multilayer flakes – which are significantly cheaper and more widely available – are perfectly suitable. Punckt proposes an analogy: "When you write with a pencil, the mark on the paper will contain some graphene. But in this case, the existence of perfect monolayer graphene is unnecessary, because you just need the pencil trace to be black."
Secondly, scientists need to develop more suitable ways to characterise graphene, both during and after the production process. "An example of this is graphene produced by chemical vapour deposition. Researchers are trying to accurately determine the graphene's structure and properties as it grows," Punckt explains. The most common technique to evaluate graphene's quality is Raman spectroscopy. It has now become a standard in industry, and Graphene Flagship scientists are hopeful that it will be the key to analysing graphene mid-production. Similarly, scientists need to develop better methods to determine the chemical properties of the graphene oxide powders used to make polymer composites. "We can use a technique called X-ray photoelectron spectroscopy, but it is often complicated and expensive. Quick spectroscopic measurements would be better, but these need to be developed further."
The third challenge is that many applications of graphene are only just emerging, so a lot of the key control characteristics and key performance indicators have not yet been established. "We need detailed information about the property–performance relationships in graphene, many of which are not fully known or understood yet," Punckt continues. Scientists creating graphene-based polymer composites with a focus on mechanical strength, for example, must devote a lot of effort, in terms of planning and development, to determine the optimum type of graphene that results in the most desirable mechanical properties.
Finally, it is important to consider the perspective of the sellers. "Graphene is used as a marketing term," Punckt rationalises. If we were to grade graphene based on surface quality and number of layers, 'Grade A' graphene would of course sell better than lower grades – so this sort of scheme is unlikely to be agreed upon. This is not unjustified: graphene of allegedly lower grades would indeed be the best choice for certain applications. For example, transistors and batteries have near opposite requirements when it comes to structure and quality of the material. "We need to define a graphene classification scheme that is clear and quantifiable, and that satisfies both researchers and commercial graphene sellers. This really highlights the importance of the Graphene Flagship's Standardisation Committee."
The Graphene Flagship Standardisation Committee
The Committee acts as the link between Graphene Flagship research and the international standardisation committees, ISO and IEC. Members of the Graphene Flagship committee are granted personal membership of ISO Technical Committee 229 (Nanotechnologies), and formally liaise with IEC Technical Committee 113 (Nanotechnology for Electrotechnical Products and Systems). In total, over 35 graphene-related standardisation projects have published documents describing graphene-related international standards or technical specifications, nine of which were led by the Graphene Flagship Standardisation Committee.
These documents provide a set of agreed-upon standards for graphene and layered materials. "This is the first strong step in the right direction, and we hope that this first set of standards will set a precedent," Punckt says. There is still a mountain to climb before a universal set of standards for graphene are in place, but these documents will be the first of many. "We hope that these standards will help to establish trust and confidence from industry, opening the door for more graphene-based materials and layered materials to be standardised – facilitating the commercial adoption of graphene technologies."
For more information on the standardisation of graphene and layered materials, please contact Dr Christian Punckt or Dr Thurid Gspann, Senior Researcher at Karlsruhe Institute of Technology and Manager of the Graphene Flagship Standardisation Committee.
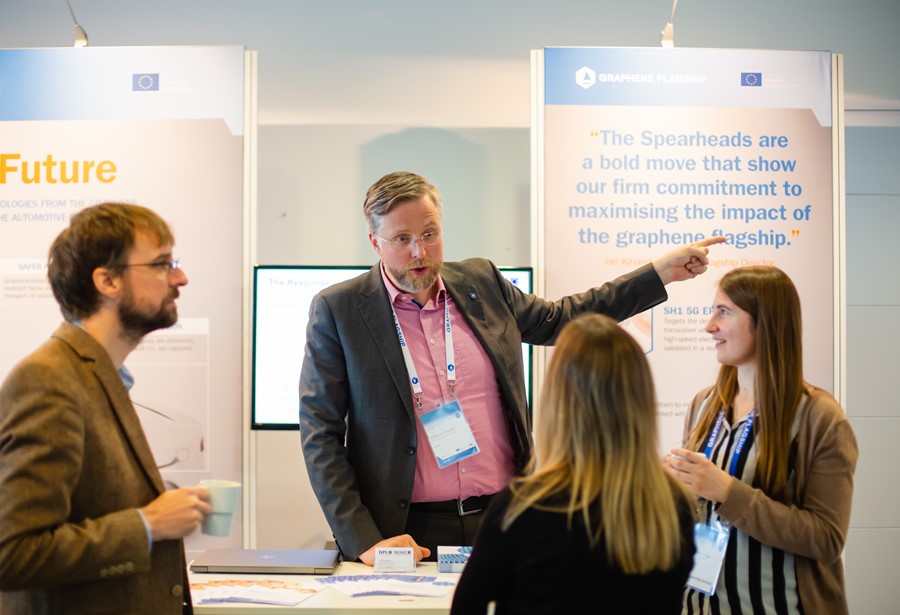