Graphene applications: Circuitbreakers
The CircuitBreakers Spearhead Project, funded by the Graphene Flagship and led by industrial partners ABB, Nanesa and GraphMaTech AB, is developing a first-of-their-kind grease-free, maintenance-free, low-voltage circuit breakers for fault protection in key parts of the electrical grid.
Circuit breakers are safety-critical components, but as the greases used in conventional circuit breakers can decompose over time, businesses are faced with recurring and costly maintenance.
To tackle this problem, the CircuitBreakers Spearhead Project, funded by the Graphene Flagship and led by industrial partners ABB, Nanesa and GraphMaTech AB, is developing a first-of-their-kind grease-free, maintenance-free, low-voltage circuit breakers for fault protection in key parts of the electrical grid.
Graphene-enhanced CircuitBreakers could be a longer lasting, more sustainable alternative to safeguard the electrical grid from faults and hazards. Many different parts of the grid use circuit breakers, like data centres, wind farms, and photovoltaic plants, as well as many different areas of industry.
Low-voltage air circuit breakers are the most common, and they are usually lubricated with grease. They work by disconnecting sensitive electrical components from the grid in case of adverse events like lightning strikes or falling trees. However, the grease between their moving components degrades over time, which can potentially lead to device failure – meaning regular maintenance and regreasing are necessary.
Graphene-enhanced CircuitBreakers replace the grease-based lubrication with a self-lubricating composite combining metal and graphene. The scientists behind the CircuitBreakers project optimised an innovative new coating method based on electroplating. The method is cost-efficient, scalable up to a hundred litres, and can be applied to an industrial setting.
When applied to moving parts and points of contact, the metal-graphene coating quickly builds up a lubricating film that protects the surfaces from oxidation. Thanks to graphene’s strongly lubricating properties, the mechanical parts can slip and slide smoothly against each other with very little friction. The coating withstands a range of humidities and is resistant to corrosion, preventing degradation for longer, and increasing device lifetime, without requiring reapplication or maintenance.
Graphene-enhanced CircuitBreakers could be a longer lasting, more sustainable alternative to safeguard the electrical grid from faults and hazards.
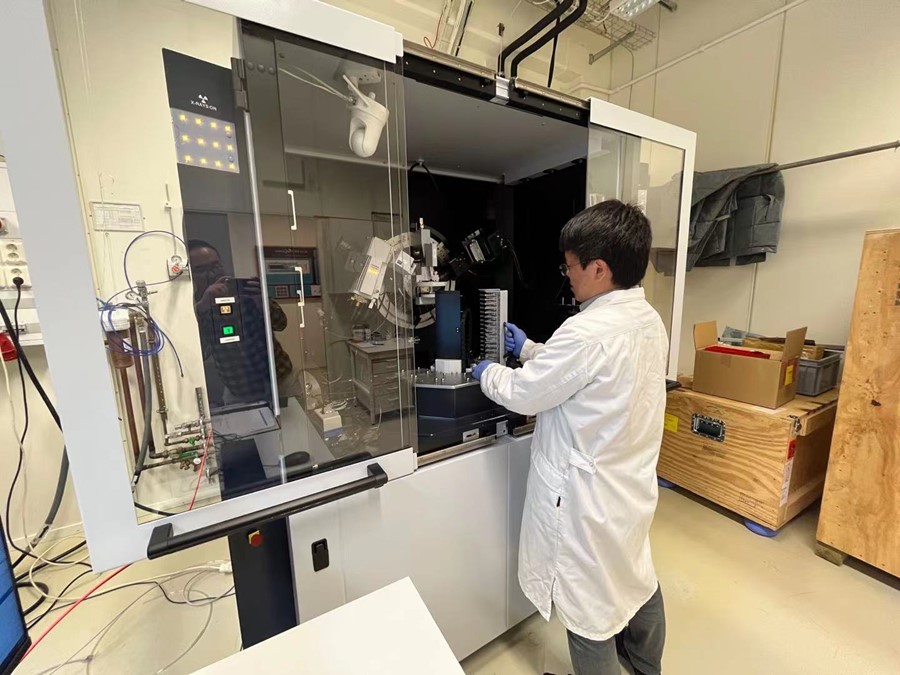
The scientists behind the CircuitBreakers project optimised an innovative new coating method based on electroplating.