Integrating graphene into textiles for lightweight, soft and conductive fabric
Associate Member Grafren AB develops smart textiles using their newly-patented method to separate high-quality graphene flakes.
Grafren AB is a Graphene Flagship Associate Member specialised in the production of graphene flakes and their applications to textiles and other products. Their first patent was recently granted, so we took the opportunity to sit down and chat with Grafren’s CEO, Erik Khranovskyy, to discover more about their strategies and plans to turn simple textiles into smart, electronic products.
How did you start this journey?
Grafren AB spun off from Graphene Flagship Associate Member Linköping University, Sweden, in 2018. Our special interest has always been in graphene flakes, because they are affordable and have plenty of potential applications.
We believe in the importance of the quality of graphene. This can make the difference between a successful and failed demonstration of graphene-based materials. Having the right thickness of graphene is essential to benefit from its outstanding properties, but this is always a challenge with graphene flakes: the manufacturing method may result in a mixture of flakes with various thicknesses and lateral sizes.
In the case of small volumes, filtering or centrifugation can separate flakes into fractions, but these methods are impractical for large volumes, as they require a lot of energy and time investment. I strongly believe that the post-synthesis treatment of graphene flakes dispersion is one of the biggest obstacles for graphene commercialisation, since it has a large impact on its production costs.
Is your recently patented method going to tackle this problem?
Yes, we developed an innovative method to treat large volumes of graphene dispersions and separate graphene flakes into different fractions based on their thickness and lateral size.
The main benefit of this technology is that it allows for the separation of thinner flakes from flakes thicker than 10 atomic layers, bulk inclusions and other contaminants. For our company, this first patent is crucial, because the method enabled the preparation of water dispersions of single and double-layer flakes of graphene oxide and graphene. The thickness of the material is directly related to the flakes’ hardness and their bending ability.
The method uses gravity, and is based on the difference between the floatation and sedimentation speed of graphene and graphene oxide flakes in the liquid dispersion. It is economically viable for large-scale graphene production, since it requires less energy and minimum labour.
What are you working on?
Thanks to our separation method we were able to obtain high-quality graphene flakes and work on our main product: electrically conductive textiles. We developed an innovative way to incorporate graphene flakes into the depth of the fabric, wrapping every individual fibre and creating a conductive “skin” with controlled electrical conductivity. We filed a patent for this invention in 2020, which is now pending. This would be Grafren’s second patent.
We are growing our products’ portfolio with a customer-centred approach, testing diverse textile materials and planning the scale-up. The size of fabric we can manufacture is approximately 60 x 40 cm2 at present, but we aim to reach 120 x 60 cm2 by April 2021. Full roll-to-roll production is expected by the end of 2021.
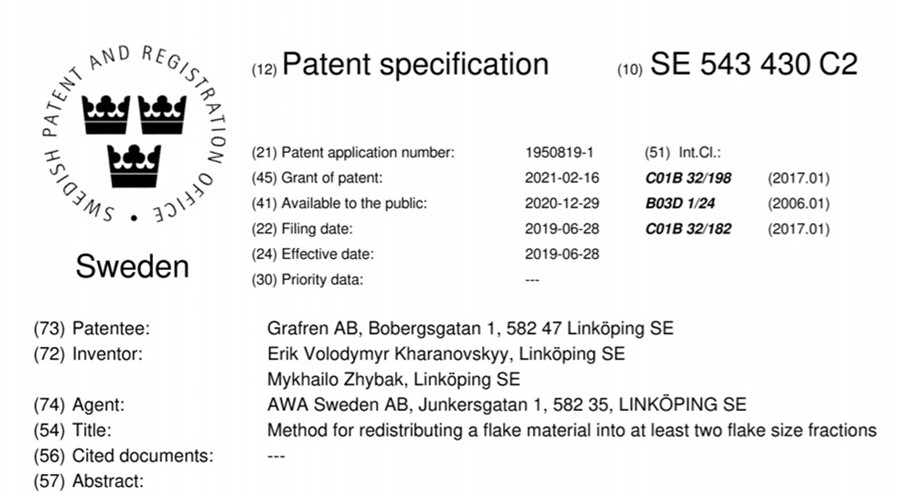
A Swedish National Patent for Grafren AB’s method was granted on 16 February 2021. They filed a PCT application in 2020. Grafren AB
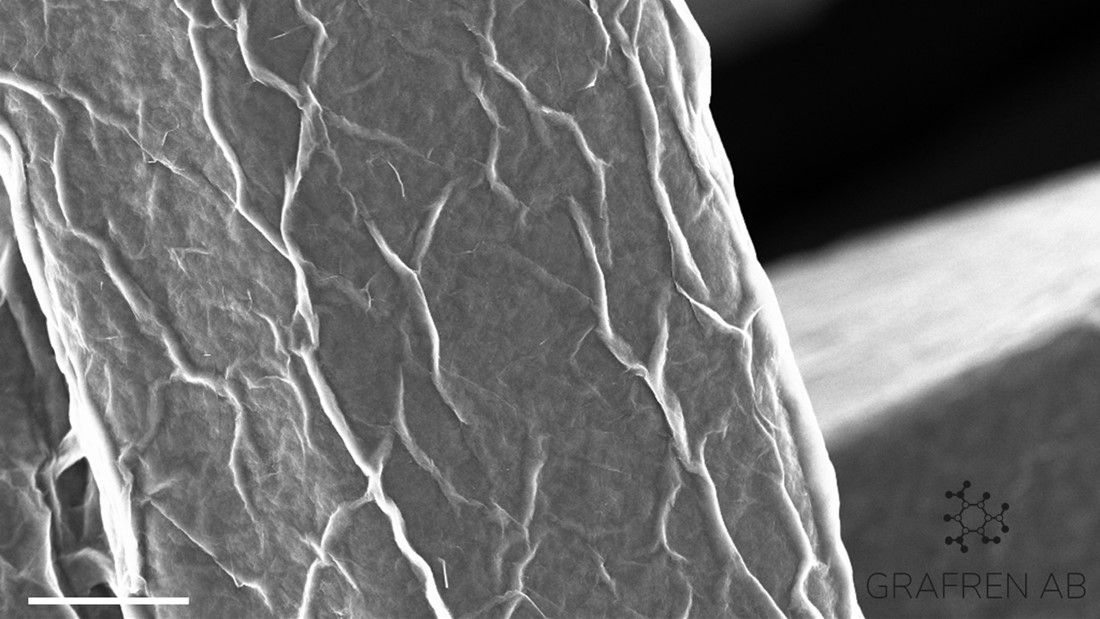
Scanning Electron Microscopy image of a graphene-coated individual fibre in electrically conductive fabric. Credit: Grafren AB
Which are the suitable application areas for these textiles?
We can make any textile or fibered material, even glass fibres, conductive. For example, conductive glass fibres are especially interesting for smart composite materials. We are talking with companies in different sectors, including healthcare, sport, aerospace, defence, gaming, etc. We experienced interest from customers who are willing to collaborate with us, and pay for pre-pilot projects. One of these projects led to a product for sports equipment, which we plan to announce in May 2021.
What are your unique selling points?
Our conductive fabric is unique by its nature: it is still a fabric made of fibres, but every fibre is coated with the thinnest flakes. At the same time, it feels and behaves like any other fabric. It is soft, flexible, and air and moisture-permeable. Since our conductive coating contains only water and graphene, it is more environmentally friendly than others. We do not use binders. There is no glue or polymer to hold conductive components together inside the fabric. This is due to the distinctive properties of the graphene flakes, which wrap around the fibres, forming the “skin.”
The fabric is extremely lightweight: two grams of graphene loading per square meter of polyester fabric allow for a high resistance of 500 Ohm/m2. This is an advantage over other materials, which require binders and are therefore hard, brittle and at least 10 times heavier.
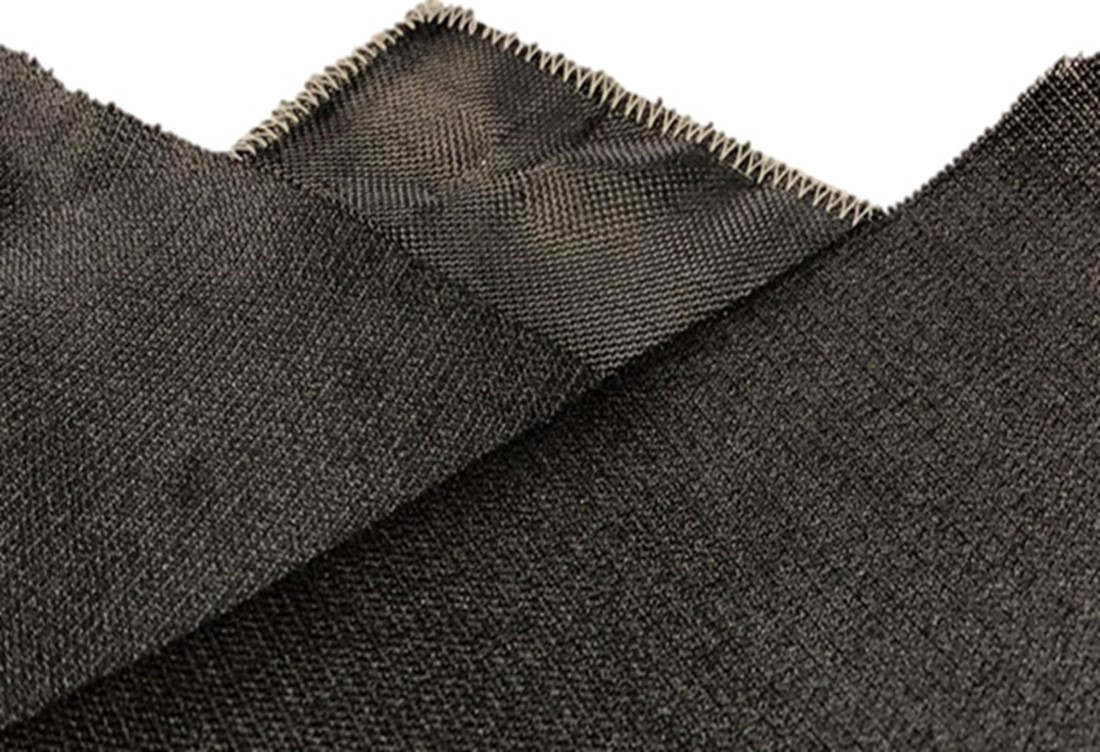
Examples of the electrically conductive fabric made by Grafren. Credit: Grafren AB
Why did you decide to join the Graphene Flagship in 2020?
The Graphene Flagship unites world-leading researchers in graphene and layered materials. Dreaming big and aiming high, we believe that collaboration is the only way to innovate. That is why we are here, collaborating already with several partners of Graphene Flagship consortium.
Which are your future plans?
We work on the development of electrically conductive fabrics based on graphene, but our next step is the opposite: insulation. Almost every application of conductive fabrics requires partial insulation of the conductive area. Since conduction is realised on an individual fibre basis, the same goes for insulation. For this reason, we consider applying a layered material with high insulation ability, such as hexagonal boron nitride, to the graphene-coated fibres. Following the same coating technology for other layered materials’ flakes as that for graphene flakes, we could then realise multi-coatings on individual fibres, while preserving the textile structure, porosity and permeability. Such coatings would create a printed circuit board (PCB) integrated into a piece of fabric.
This will enable the future concept we aspire to establish: a Digital Textile Interface (DTI) for human-machine communication. The idea is that the integration of invisible electrodes into conventional clothes will enable the permanent monitoring and stimulation of the human body by respective sensors or actuators. It will transfer signals, such as transcutaneous electrical nerve stimulation for pain control, heat or any other kind of stimulation, to the human body. At the same time, it will monitor human health or motion, via electrodermal, electrocardiogram and other sensors, and pass this information on to the data storage or processing unit. So far, this concept has not been possible due to the limitations of the conductive electrodes on textiles, which are either painted or laminated, making them dense, non-breathable, strong and rigid. Our approach can be used for DTIs, but it requires further technology development and concept demonstration.
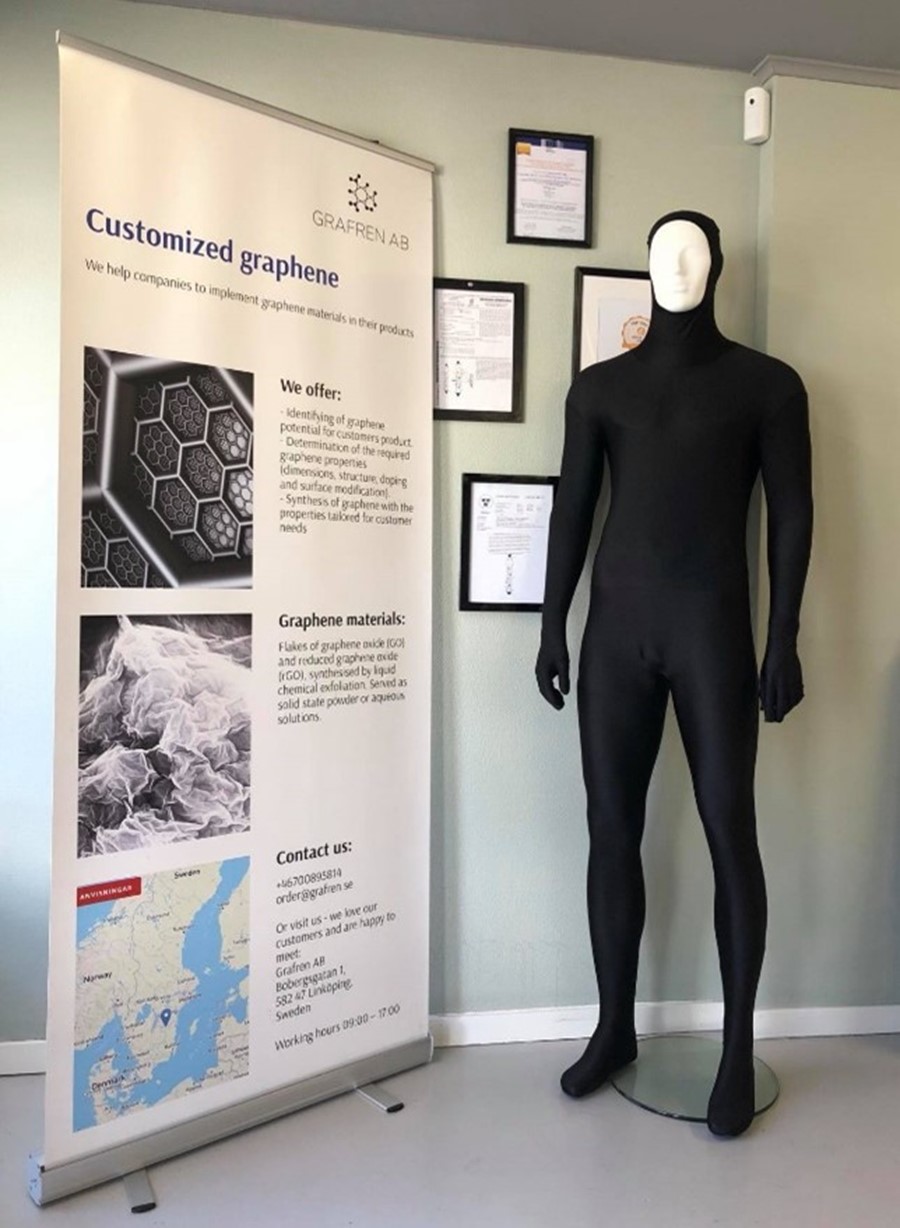
Using electrically conductive graphene-based fabric for a digital textile interface (DTI) is the future aim of Grafren AB. Image credit: Grafren AB.