Spotlight: Graphene-based gas sensors with Marko Spasenović
Interview with Marko Spasenović, Graphene Flagship Associate Member, about graphene’s role in next-generation sensors
Marko Spasenović works at Graphene Flagship Associate Member the Institute of Chemistry, Technology and Metallurgy (ICTM) in Serbia. He is an Associate Research Professor at the Center for Microelectronic Technologies, where Spasenović and his colleagues specialise in the design, fabrication, characterisation and commercial exploitation of sensors.
We spoke with Spasenović about his experience with the Graphene Flagship and his latest scientific findings – in particular, the development of a humidity sensor with an extremely fast response that is unprecedented in current technology.
When did you join the Graphene Flagship as an Associate Member, and why?
I first joined the Graphene Flagship in 2015 when I returned to Serbia after 15 years of living abroad. At the time, not only had I moved countries, but I had also joined a field of research that was new to me, and I thought: what better way to reach a new community than to join the Graphene Flagship project?
What's the benefit of joining the Graphene Flagship as an Associate Member?
The biggest gain for me was networking with experts in the field of graphene-based sensors during Graphene Flagship's Work Package meetings and Graphene Week. Presenting my work at these events and discussing with international peers really helped to clarify my vision and place it in the context of current global trends. I also established active collaborations in areas that we cannot cover on our own, which significantly widened the impact of my work.
What do you specialise in?
We specialise in producing thin films that are made of liquid-phase exfoliated graphene. We use the the Langmuir-Blodgett method, where graphene flakes at the water-air interface self-assemble into a thin film. This method has not been pursued very much by other groups, but we showed that the resulting films can have reasonable sheet conductivity, while retaining high optical transparency, which is desirable for transparent flexible electronics.
We also noticed that these films react strongly to the presence of various chemicals. We attributed the high reactivity to an abundancy of reactive edges and the small film thickness, and we followed up on these discoveries by utilising the sheets as active materials in gas sensors.
What are you working on at the moment?
One of my objectives is to construct graphene-based multiparameter sensors to simultaneously measure the presence and concentration of trace gases, relative humidity, temperature and strain. We envision a fully working sensor that is worn, for example, on the transparent face shield of first responders like firefighters, or even astronauts. The sensors could be also applied to transparent touchless control panels.
On the road to multiparameter sensors, our first achievement was the construction of flexible, fast and nearly 80% transparent humidity sensors. This type of device has traditionally been used to monitor atmospheric vapour, but the unprecedented speed of our sensors foreshadows new applications. In healthcare, ultrafast humidity sensing could be used to monitor human respiration due to the high level of water vapour in the breath. In electronics and robotics industries, sensors in touchless control interfaces could detect humidity clouds that form near the human body.
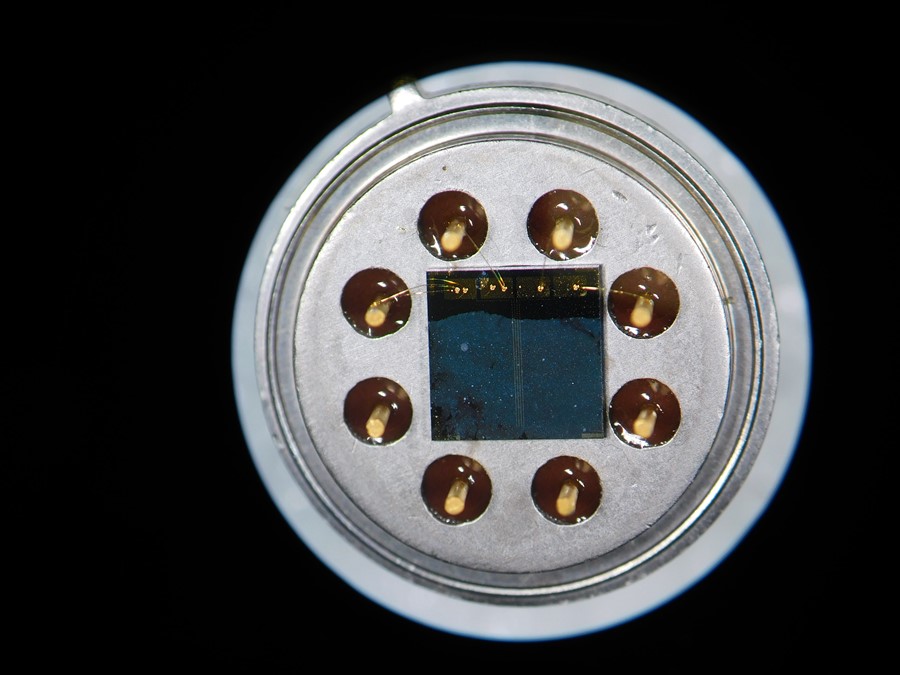
Graphene gas sensor developed by Marko Spasenović and colleagues. Credit: Marko Spasenović
Why do you think that graphene offers the best properties for these sensors?
For certain applications, it is advantageous to have sensors on a transparent substrate, for example on transparent masks. Graphene is therefore the material of choice. Furthermore, current sensors are not fast enough to monitor human respiration and skin humidity. Sensors made of established materials, as well as emerging composite materials and nanomaterials like zinc, palladium and tin oxide, have response rates between five and 50 seconds. On the contrary, graphene and graphene oxide can offer response rates between a dozen milliseconds and a few seconds, depending on the method of production. The humidity response times of our sensors are as low as about 30 milliseconds.
What's next for your research?
We are now building a lab where we can control environmental parameters like humidity, gas composition and temperature, and introduce trace amounts of gases to test the sensors' response. The collaboration with Graphene Flagship partner Bundeswehr University of Munich in Germany has been instrumental in this regard, because they have a similar laboratory and years of experience in gas sensing.
Once the new lab is ready, we will carefully study the effect that each environmental parameter has on our sensors, explain why the sensors react in the way they do, and devise algorithms to selectively distinguish between the effects of temperature, humidity, strain and the presence of gases in the environment.
I saw that you're applying graphene to acoustics, as well. How does this work?
We are developing microphones with vibrating membranes made of graphene. It is not often thought about, but graphene is an excellent material for acoustics applications. Thanks to its light weight, graphene responds strongly to changes in the acoustic pressure, while the strength of the graphene membranes enables large bandwidths. Our first prototype outperformed traditional nickel-based microphones, with a 12dB enhancement of sensitivity. Under optimal conditions, graphene microphones could cover both audible and ultrasonic parts of the spectrum in a single device.
We found out that few-layer graphene grown on molybdenum by Graphene Flagship partner Delft University, Netherlands, is the best choice for acoustic membranes. It is mechanically robust because it has very few wrinkles. It is better than single-layer graphene and multilayer graphene grown on nickel, but thin enough to show valuable graphene properties. Together with our Graphene Flagship partners, we are pursuing on-chip integration and the miniaturisation of graphene microphones.