Life cycle assessment of graphene and related materials
Graphene can be produced using a range of methods, but what are the most sustainable options? To answer this question, Graphene Flagship researchers published three studies related to the sustainable production of graphene related materials and their life cycle assessment – the best tool to evaluate the environmental footprint of a product or material.
Reviewing different production methods
The different production methods for graphene related materials (GRMs) can vary depending on your choice of reactants, solvents and processing parameters. For this reason, even small adjustments in the manufacturing process can decrease the environmental footprint of GRMs.
Led by Cinzia Casiraghi, researchers from Graphene Flagship Partner University of Manchester, UK, and colleagues from the University of Milano-Bicocca, Italy, found that the environmental impact of chemical oxidation/reduction and exfoliation techniques can be significantly improved through higher acid and solvent recovery rates. Chemical vapour deposition (CVD) methods can become more sustainable through higher heat transfer efficiencies and more efficient consumption of precursor gases (ideally derived from renewable feedstock, such as biomass). Finally, the environmental footprint of GRM growth on silicon – an energy-intensive process by design – benefits from the use of renewable energy sources.
“The life cycle assessment (LCA) allows us to identify opportunities for improvement along the life cycle of material production processes. For example, our analysis of GRM production shows that hotspots will vary depending on the production route, this could either be the carbon source, the energy requirements, or the choice of solvents and reagents needed,” LCA expert Rosa Cuéllar-Franca from the University of Manchester explained during her webinar entitled “Life cycle environmental impacts of graphene production” organised by the Innovation Work Package on 6 October 2022.
The study also highlights the need to improve the type and quality of data associated to graphene production. It will be increasingly important to compare different production routes and applications, as graphene reaches the market.
It is very important to discuss sustainable development of advanced materials at the early stages of their commercial exploitation.
University of Manchester, UK
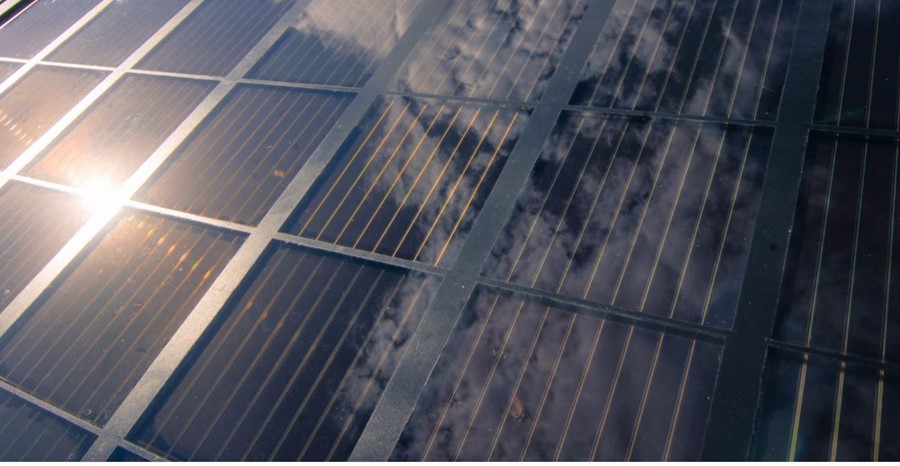
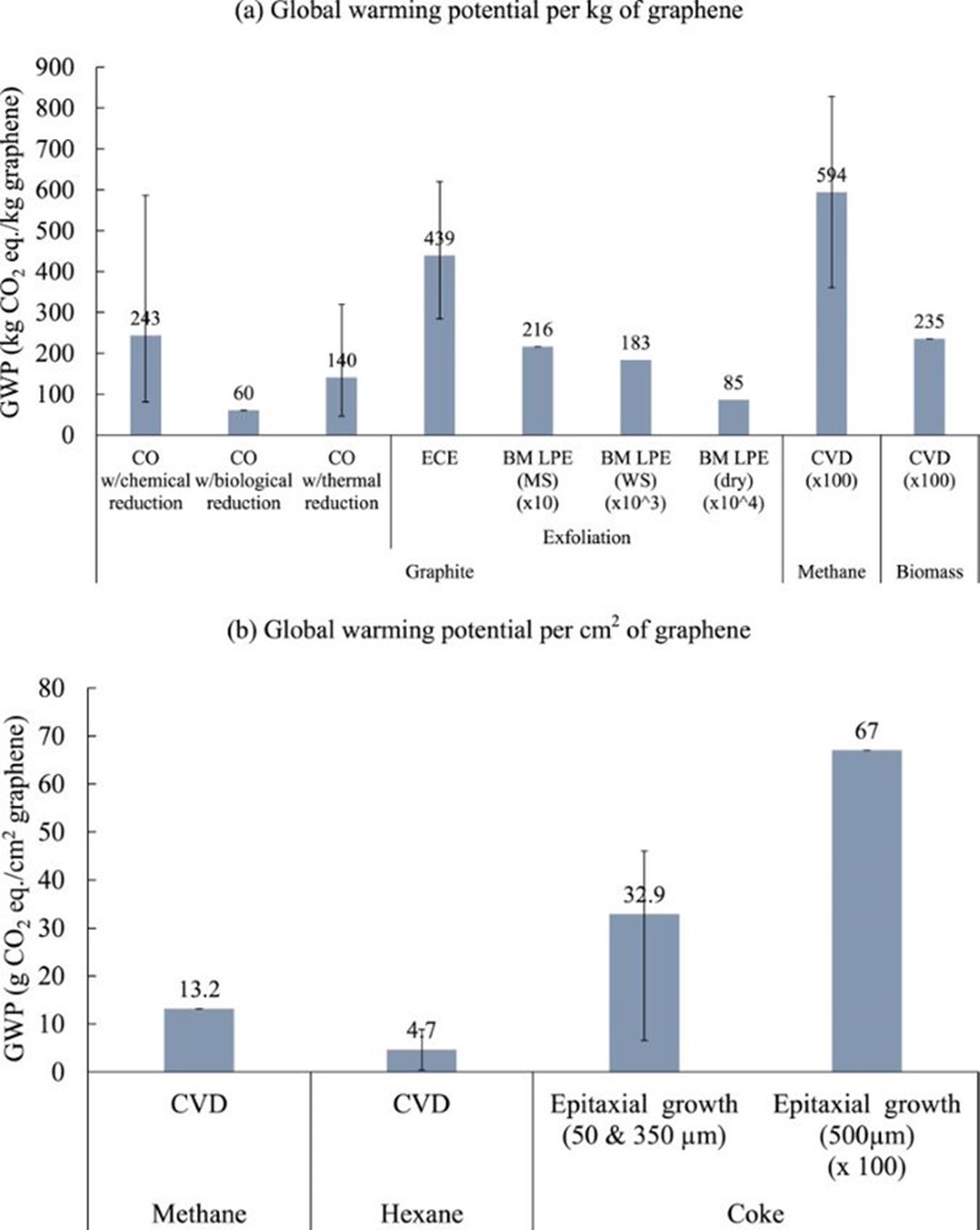
Global warming potential (GWP) for several graphene production processes, expressed (a) per kg graphene and (b) per cm2 graphene. Ball milling (BM) results are reported in melamine solution (MS), water solution (WS) and on a dry basis. Epitaxial growth results are reported in terms of the SiC wafer thickness. CO: chemical oxidation; ECE: electrochemical exfoliation; LPE: liquid phase exfoliation; CVD: chemical vapour deposition. Credit: 2D Mater. 2021
The ball milling process
In another study, LCA experts from Graphene Flagship Partner EMPA, Switzerland, measured LCA-relevant data for the ball milling process – a method used to exfoliate graphite into few-layer graphene. They compared 38 lab-scale pathways to producing single and few layer graphene and graphene oxide. They focused on cradle-to-gate LCA, which considers the sustainability of a product from its resource extraction (cradle) to the factory gate, before it reaches the consumer.
“Our analysis shows that graphene-based materials can be environmentally beneficial in some applications, but there is a need for more accurate data on manufacturing steps to identify the most interesting options,” says Didier Beloin-Saint-Pierre from EMPA.
Our analysis shows that graphene-based materials can be environmentally beneficial in some applications, but there is a need for more accurate data on manufacturing steps to identify the most interesting options.
EMPA
Applying LCA to the first graphene-enabled solar farm
The cradle-to-gate LCA and environmental profile of the first solar farm based on perovskite solar panels enabled by graphene and other layered material was evaluated by researchers from Graphene Flagship Partners Hellenic Mediterranean University, Greece, University of Rome Tor Vergata, Greatcell Solar Italia SRL, IIT, National Research Council and BeDimensional S.p.A., Italy.
“The team demonstrated the commercial potential of this technology in terms of both energy and environmental performance. The environmental footprint is lower than the present European electricity mix, and even better than some of the energy mix scenarios foreseen by the European energy roadmap 2050,” says Emmanuel Kymakis, from the Hellenic Mediterranean University.
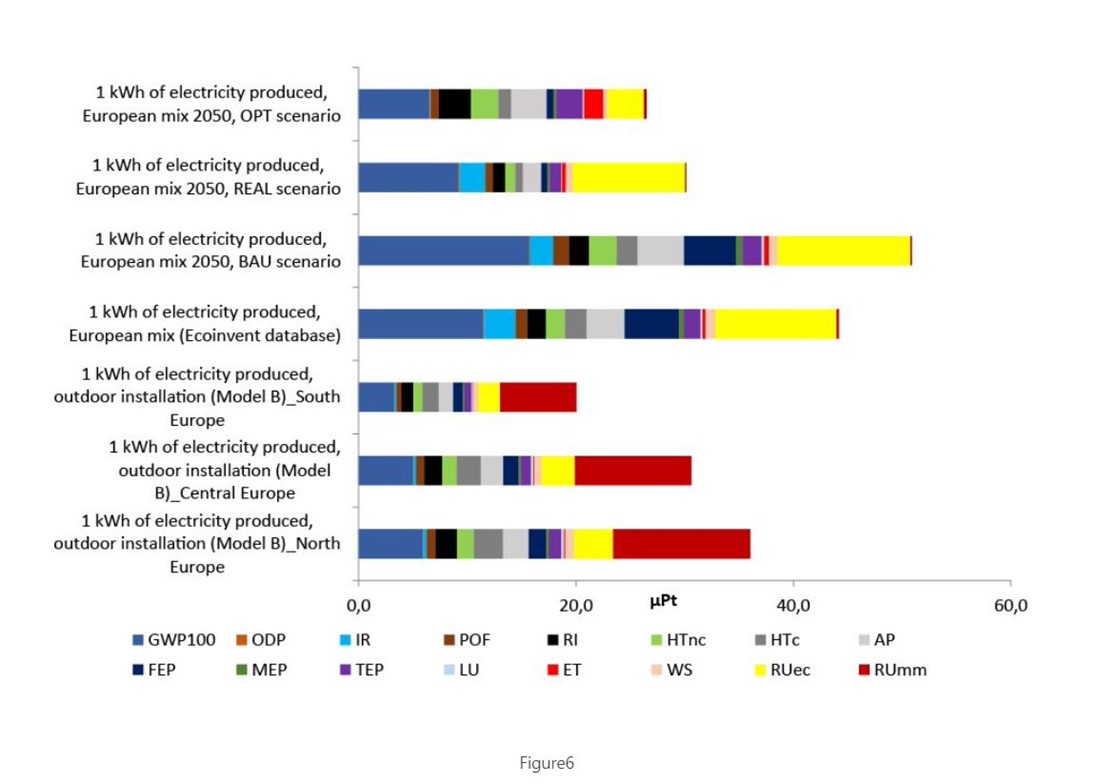
Environmental footprint of optimised graphene-enabled solar farm (Model B) if installed in North, Central and South Europe, current European electricity mix (Ecoinvent), and 2050 European electricity mix based on business-as-usual (BAU), realistic (REAL) and optimistic (OPT) scenarios. Perovskite-graphene panels installed in South Europe have the lowest environmental impact. The Environmental Footprint 2.0 method used to perform LCA considers the following 16 environmental categories: Climate change (GWP100), ozone depletion (ODP), ionising radiation (IR), photochemical ozone formation (POF), respiratory inorganics (RI), non-cancer human health effects (HTnc), cancer human health effects (HTc), acidification terrestrial and freshwater (AP), eutrophication freshwater (FEP), eutrophication marine (MEP), eutrophication terrestrial (TEP), land use (LU), ecotoxicity freshwater (ET), water scarcity (WS), resource use, energy carriers (RUec) and Resource use, mineral and metals (RUmm). Credit: Int J Life Cycle Assess. 2021
Looking at the future
Rosa Cuéllar-Franca points out that these efforts are only the beginning towards understanding the environmental impacts of GRM production: “The major challenge is the lack of data on the commercial production of GRMs to conduct representative LCA studies, which is not surprising considering the cutting-edge nature and competitiveness of the field. LCA studies requires highly sensitive information that companies might not be willing to share openly.”
Furthermore, most LCA studies on GRMs are from cradle-to-gate rather than cradle-to-grave, which excludes the application and end-of-life stages. It is recommended that future studies consider the full life cycle of these materials, especially their application and functionality aspects, as this will allow us to properly understand their actual benefits. “For example, the relatively high environmental impacts of producing a material could be compensated by an extended service life of an enhanced product with such material,” explains Cuéllar-Franca.
The team demonstrated the commercial potential of this technology in terms of both energy and environmental performance. The environmental footprint is lower than the present European electricity mix, and even better than some of the energy mix scenarios foreseen by the European energy roadmap 2050.
Hellenic Mediterranean University