The layered materials’ trove
Graphene and layered materials put an end to the treasure hunt for rare earths and scarce materials, paving the way to sustainable electronics
On the isolated coast of southwest Greenland, the abandoned mining town of Ivigtut is eerily baron. The site was once home to a prosperous mine and was one of the world’s few sources of cryolite, a material used to refine aluminium, make pesticides and insecticides, and give fireworks their yellow colour. Then in 1987, the mine simply ran out.
Ivigtut mine’s demise and abandonment is a reminder of how global demand can quickly outstrip earth’s natural resources. Today, we are experiencing the same imbalance in the supply of rare minerals and the scale of their demand in the electronics industry. However, graphene and layered materials could alleviate this challenge, tackling the global material crisis.
Raw material reserves
Among the very rarest of materials used in electronics are tantalum, gallium, indium and rare earths like europium and neodimium, among a host of others. These elements are found in naturally occurring minerals that, like cryolite, cannot be recreated or replaced. Moreover, many are only present in miniscule quantities in the Earth’s crust.
The applications of these materials are unbelievably widespread. In fact, you are within just a few inches of at least one of these materials, working away to allow your smartphone or laptop to operate. What’s more, they are increasingly used in developing environmental technologies such as solar panels and batteries for electric vehicles (EVs).
The scarcity of these materials is already causing a huge surge in their cost. The price of lithium, used in modern day batteries, has increased by 150 per cent since September 2020. Holmium, used to make magnets and alloys for sensors and actuators, has more than doubled in price; other rare earths like neodymium and praseodymium, minerals used in magnets, motors and wind turbines, have seen an increase of 73 per cent in a single year.
Costs are rising, but what happens when these raw mineral reserves run out, or become too expensive to use? Ivigtut’s depletion caused a collapse of the town’s mining community, but the potential of stopping the world’s electronics manufacturing industry — and the public’s insatiable desire for new electronics — is almost incomprehensible.
Exploring new options
While the recent data appears catastrophic, the scarcity of these rare materials is not a new concern. China, which is home to more than 90 per cent of rare mineral refining, claims that supplies of rare earth elements such as dysprosium, neodymium and lanthanum — coveted for their conductive properties and commonly used in computers — could be exhausted in just 20 years.
Some sceptics have argued that the concern about diminishing availability of rare metals is misplaced, suggesting increased mining could discover untapped reserves. While that’s possible, it cannot be relied upon.
Meanwhile, industry experts elsewhere have called for tougher rules on recycling of electronics, hoping to make better use of the rare metals in disused technology. In a recent report, European project Cewaste explained that recycling should be mandatory for the crucial raw materials present in electronics.
But, even if the industry did have a robust recycling mandate in place, shouldn’t we be looking for better, more easily obtainable alternatives?
Graphene for electronics
The Graphene Flagship has been exploring the potential of graphene for electronics since the project’s inception almost a decade ago. Boasting impressive flexibility, strength and conductive properties that surpass the potential of copper, the material has much to offer an industry that is currently grappling with ever-escalating costs of other metals.
"[Graphene] is the thinnest material, making it an excellent choice for new sensing devices,” explained Maria Smolander, research team leader from Graphene Flagship partner VTT, Finland. “It's also a more sustainable solution, as graphene-based circuits can be printed without requiring rare or precious metals.”
In fact, in January of this year, Graphene Flagship researchers proved the potential of graphene for use in touch screen sensors. Their study demonstrated the fabrication of organic light-emitting diodes (known as OLEDs) with a monolayer of graphene in the anode. This method replaced the use of indium tin oxide, a key part of touch screens that is currently listed as a critical raw material in Europe.
This study is a promising breakthrough — and a necessary discovery should the world need to wean itself from rare minerals in electronics. Despite the potential, there are some barriers to widespread adoption of graphene for electronics.
Crucially, wafer-scale integration of graphene is necessary for the electronics industry to transition to commercial use of graphene. This process will be accelerated by initiatives such as the European Commission’s 2D Experimental Pilot Line, part of the Graphene Flagship, which is dedicated to the improvement and scaling-up of the wafer-scale integration process.
Change for the future
Finding alternatives to rare minerals is crucial for the future of the electronics industry — and for the planet. The International Energy Agency calculated that, if the world is to reach net zero greenhouse gas emissions in 2050, the demand for critical materials and rare earths will be six times higher than it is today.
In fact, demand for lithium alone will be 40 times higher in 2040 because of its use in batteries — crucial for EVs and other energy storage applications.
While it’s likely that many of earth’s rare minerals will follow the fate of cryolite and become decimated in time, the world’s electronics industry must continue thriving to serve our growing population and help develop technologies for a greener future. We’re confident that graphene is the answer.
There are 800 MILLION tons of recoverable graphite on earth
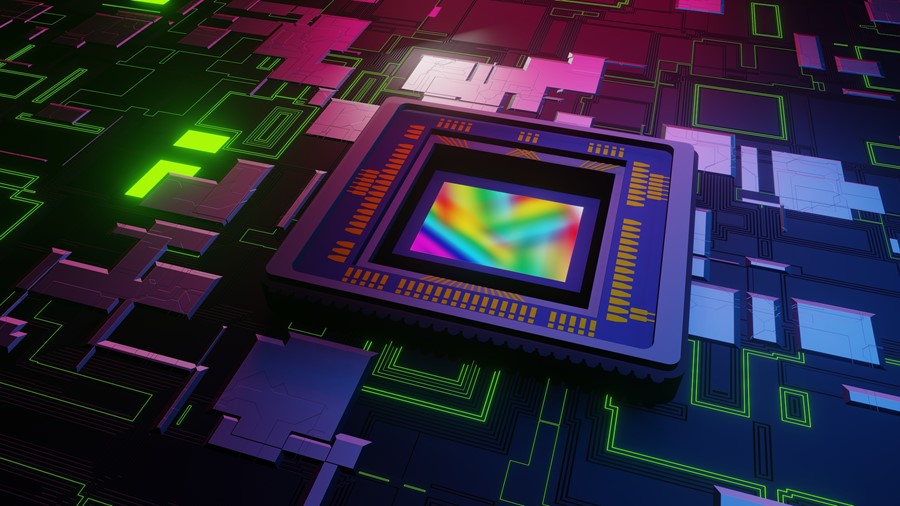
Wafer-scale integration of graphene is necessary for the electronics industry to transition to commercial use of graphene.
CARBON is the 15th most abundant element in the Earth's crust